AAC Lightweight Concrete Block Machine Production Line Light Weight Block Available(different Block Size, Density) 4.2x1.2x0.6m
US $600,000.00 / set
1 set(s)Minimum order
Type:
Autoclaved aerated concrete block (AAC), lightweight concrete machine, Aac Block Prodution Line
Brick Raw Material:
concrete,cement,sand,crushed stone,fly ash,
Processing:
Brick Production Line, Brick Cutting Machine
Method:
Autoclaved Aerated Concrete, Autoclaved Aerated Concrete
Automatic:
Yes
Production Capacity (Pieces/8 hours):
50000/100000/200000 m3
Privacy Policy:
Samples are free within a certain price range
Other recommendations for your business
Contact us
Quik Detail
Type | Autoclaved aerated concrete block (AAC), lightweight concrete machine, Aac Block Prodution Line |
---|---|
Brick Raw Material | concrete,cement,sand,crushed stone,fly ash, |
Processing | Brick Production Line, Brick Cutting Machine |
Method | Autoclaved Aerated Concrete, Autoclaved Aerated Concrete |
Automatic | Yes |
Production Capacity (Pieces/8 hours) | 50000/100000/200000 m3 |
Place of Origin | Shandong, China |
Brand Name | weida |
Voltage | 380/415/440V(customerized) |
Dimension(L*W*H) | depends |
Warranty | 1 Year |
Key Selling Points | Eco-Friendly, automatic |
Brick size | 600*200*100/150/200 |
Machinery Test Report | Provided |
Video outgoing-inspection | Provided |
Core Components | PLC, Pressure vessel, Engine, Gear, motor, Bearing, Siemens standars |
Weight (KG) | 100000 kg |
Capacity | 30000M3-300000m3/year |
Color | customized |
Local Service Location | Indonesia |
Application | House Building |
Advantage | Cost Saving,light weight |
Keywords | Aac Block Autoclave |
Applicable Industries | hotels |
Showroom Location | Indonesia, India |
Condition | New |
Marketing Type | New Product 2020 |
Warranty of core components | 1.5 years |
Product Detail
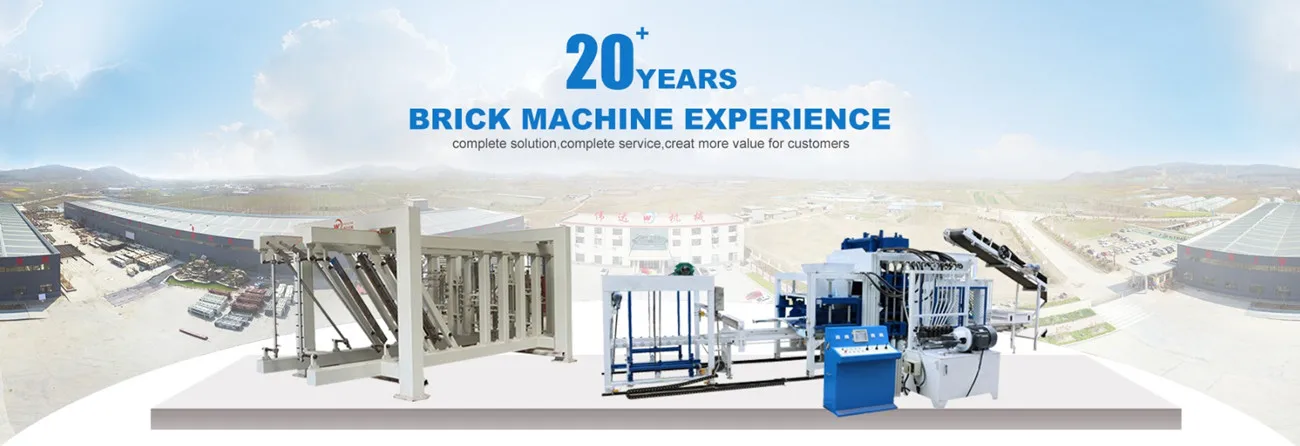
AAC Lightweight Concrete Block Machine Production Line Light Weight Block Available(different Block Size, Density) 4.2x1.2x0.6m
(1) Introduction
Aac Brick Manufacturing Plant (light brick) is the light and porous building material. It has light keeping temperature can’t burn and other advantages. It can be made into many kinds of bricks (for example: 600*200*100mm, 600*150*100mm, 600*300*200mm,600*200*150mm), they could be used industry building and common building. They are more and more popular in the world. In thefuture, they will replace the clay brick completely.(2) Advantages
Aac Brick Manufacturing Plant (light brick) is the light and porous building material. It has light keeping temperature can’t burn and other advantages. It can be made into many kinds of bricks (for example: 600*200*100mm, 600*150*100mm, 600*300*200mm,600*200*150mm), they could be used industry building and common building. They are more and more popular in the world. In thefuture, they will replace the clay brick completely.(2) Advantages
(2)Light weight
Aerated concrete density is usually 400-700kgs/m3(according the market production), same as 1/3 of clay brick and 1/5 common concrete. So, use the Light brick can reduce the weight of the build more, and also reduce the beam of roof and pillar press best.Then you can see, it can save the material and cost, it also fighting shaking.
Aerated concrete density is usually 400-700kgs/m3(according the market production), same as 1/3 of clay brick and 1/5 common concrete. So, use the Light brick can reduce the weight of the build more, and also reduce the beam of roof and pillar press best.Then you can see, it can save the material and cost, it also fighting shaking.
(3)Keeping temperature
It has many are porous, the delivery heating coefficient is 0.9-0.22W/ (m.k), the same as 1/4 or 1/5 of clay brick, so it is best materials now in the world.
It has many are porous, the delivery heating coefficient is 0.9-0.22W/ (m.k), the same as 1/4 or 1/5 of clay brick, so it is best materials now in the world.
Aac Brick Manufacturing Plant Working proccess
1. Raw material: Store the fly-ash (tailings etc), lime and gypsum after milling to the needed fineness (200 mesh)
2. Mixing the fly-ash, cement, lime, gypsum and water in the pot after batching.
3. Promote the slurry temperature to 40-50 degree by steam, and mill with aluminum powder for 1min.
4. Pour the slurry into the mould, and still in the curing room for frothing in 2-2.5h.
5. Cut it in to needed size by the cutter after the slurry approach the cutting intensity, and place the block on the trolley.
6. Autoclaved curing after the trolley enter into the autoclave (vacuum, rise the pressure, keep the pressure, reduce the
pressure),keeping the constant pressure 1.2MPa. The whole process needs about 12h.
7. The products out of the autoclave are placed in a stack. We can recycle the scrap and the waste water from the whole
production.
2. Mixing the fly-ash, cement, lime, gypsum and water in the pot after batching.
3. Promote the slurry temperature to 40-50 degree by steam, and mill with aluminum powder for 1min.
4. Pour the slurry into the mould, and still in the curing room for frothing in 2-2.5h.
5. Cut it in to needed size by the cutter after the slurry approach the cutting intensity, and place the block on the trolley.
6. Autoclaved curing after the trolley enter into the autoclave (vacuum, rise the pressure, keep the pressure, reduce the
pressure),keeping the constant pressure 1.2MPa. The whole process needs about 12h.
7. The products out of the autoclave are placed in a stack. We can recycle the scrap and the waste water from the whole
production.

Aac Brick Manufacturing Plant Raw Material dealing process.
Put the sand into ball mill to grinding into the slurry powder, after milling, pump into slurry storage tank
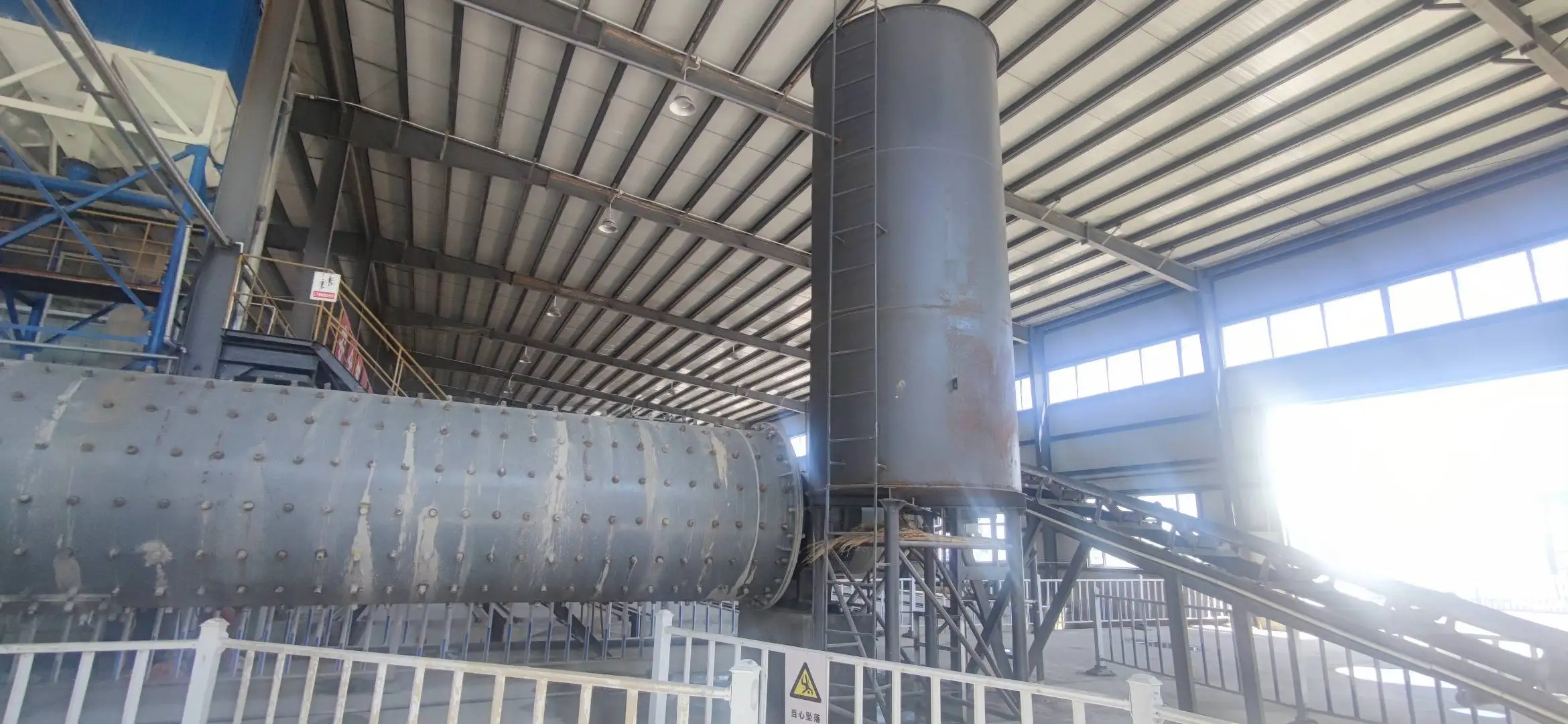
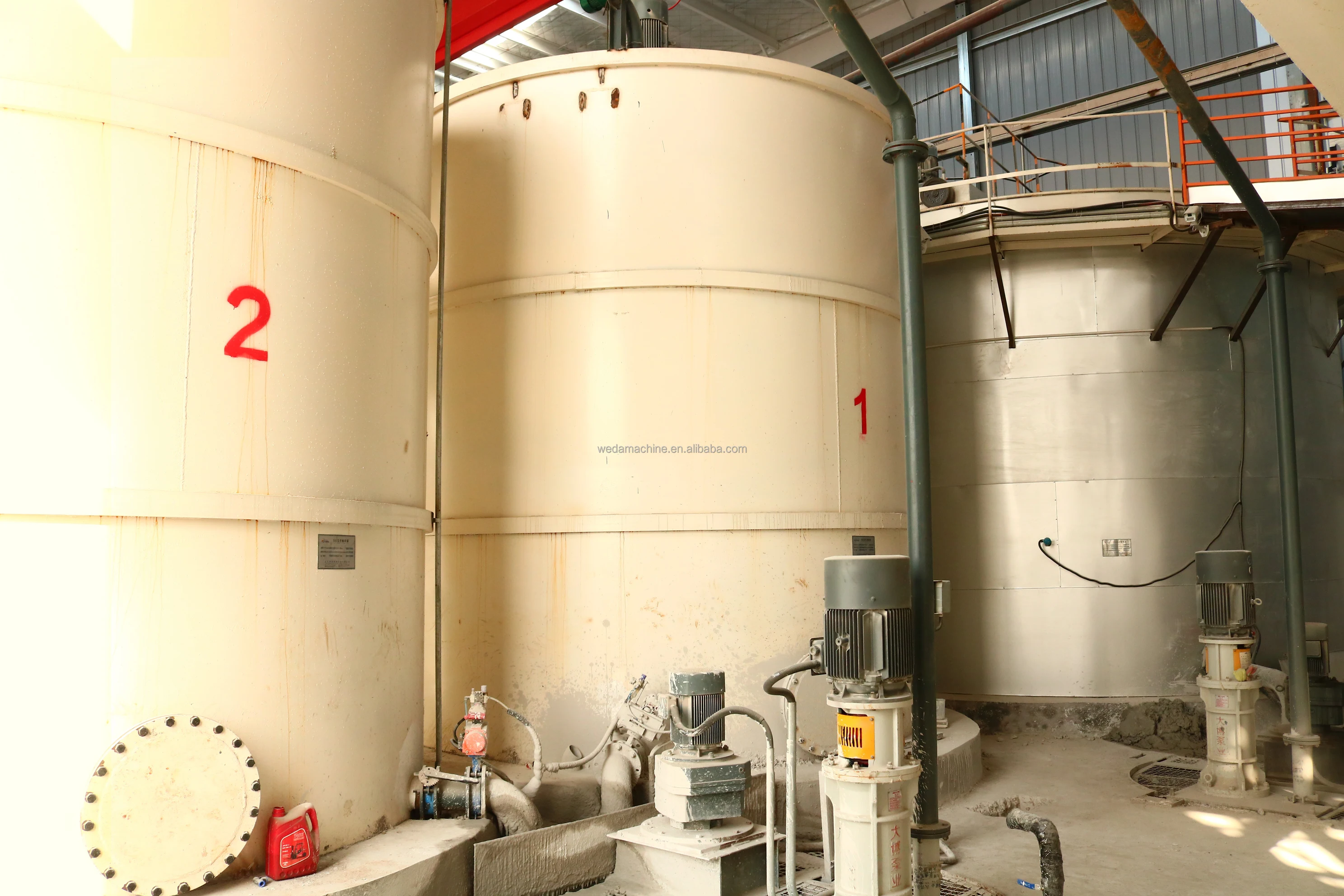
Aac Brick Manufacturing Plant Batching, mixing and pouring process.
The lime, cement will convey by conveyor to the dry powder measure scale to measure separately. The slurry (fly ash or grinded sand) is transported by slurry pump then to the automatic weighing hopper; the dry powder and slurry put into the pouring mixer, then pouring into the mould.
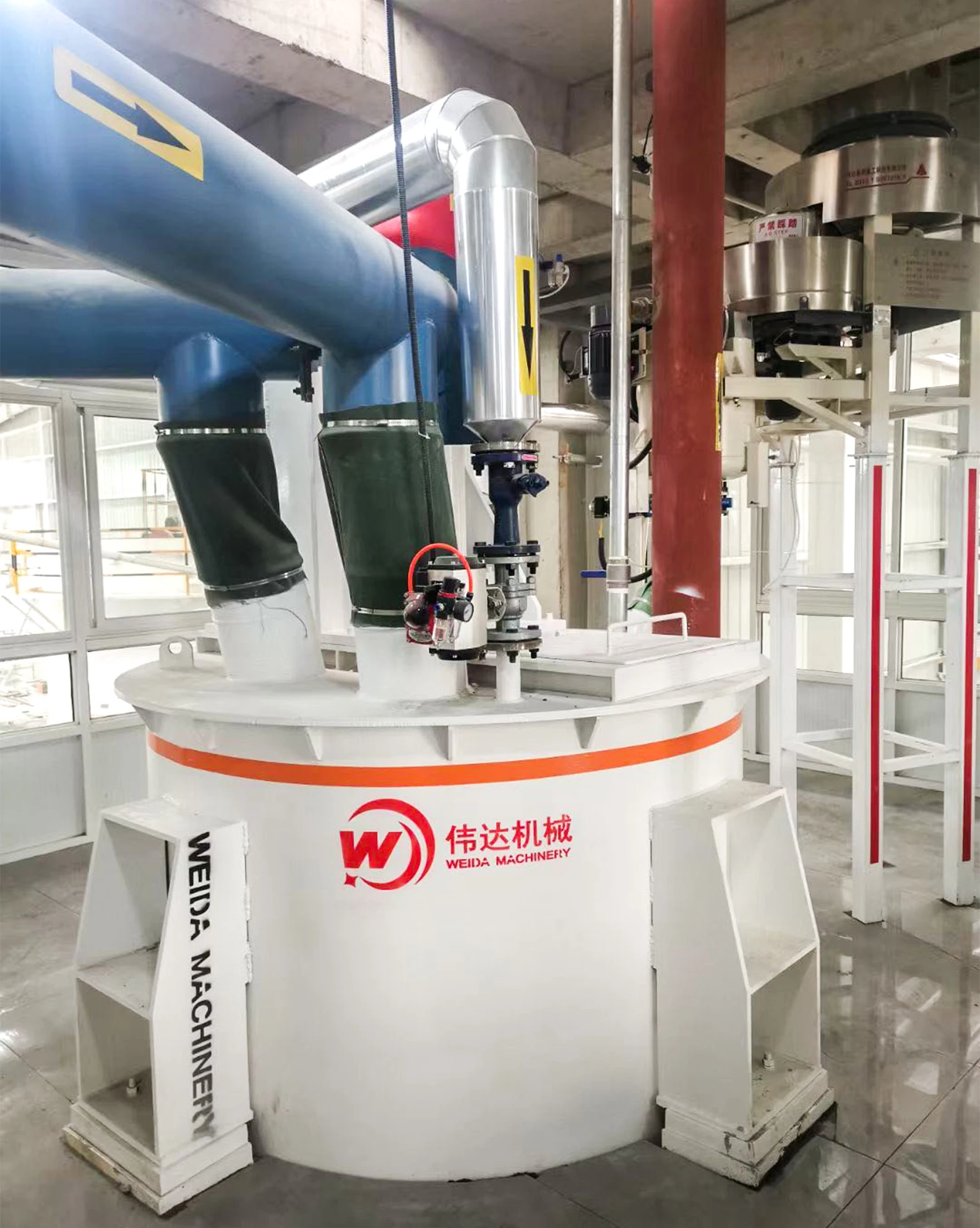
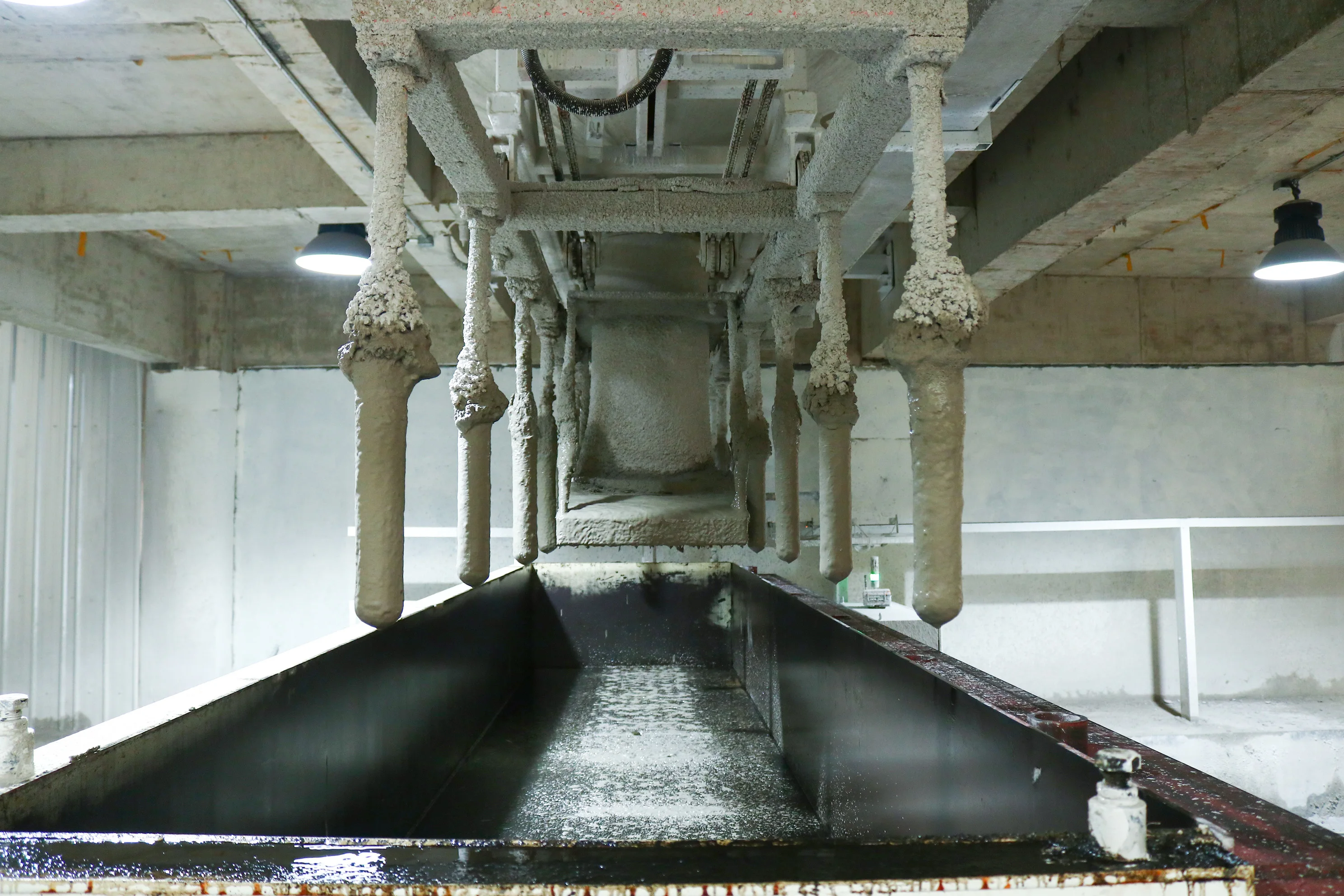
Aac Brick Manufacturing Plant Pre-Curing process.
After slurry pouring into the mould, put the mould box into the curing room with 50~70℃. After 1-2 hours curing, the blocks become solid..
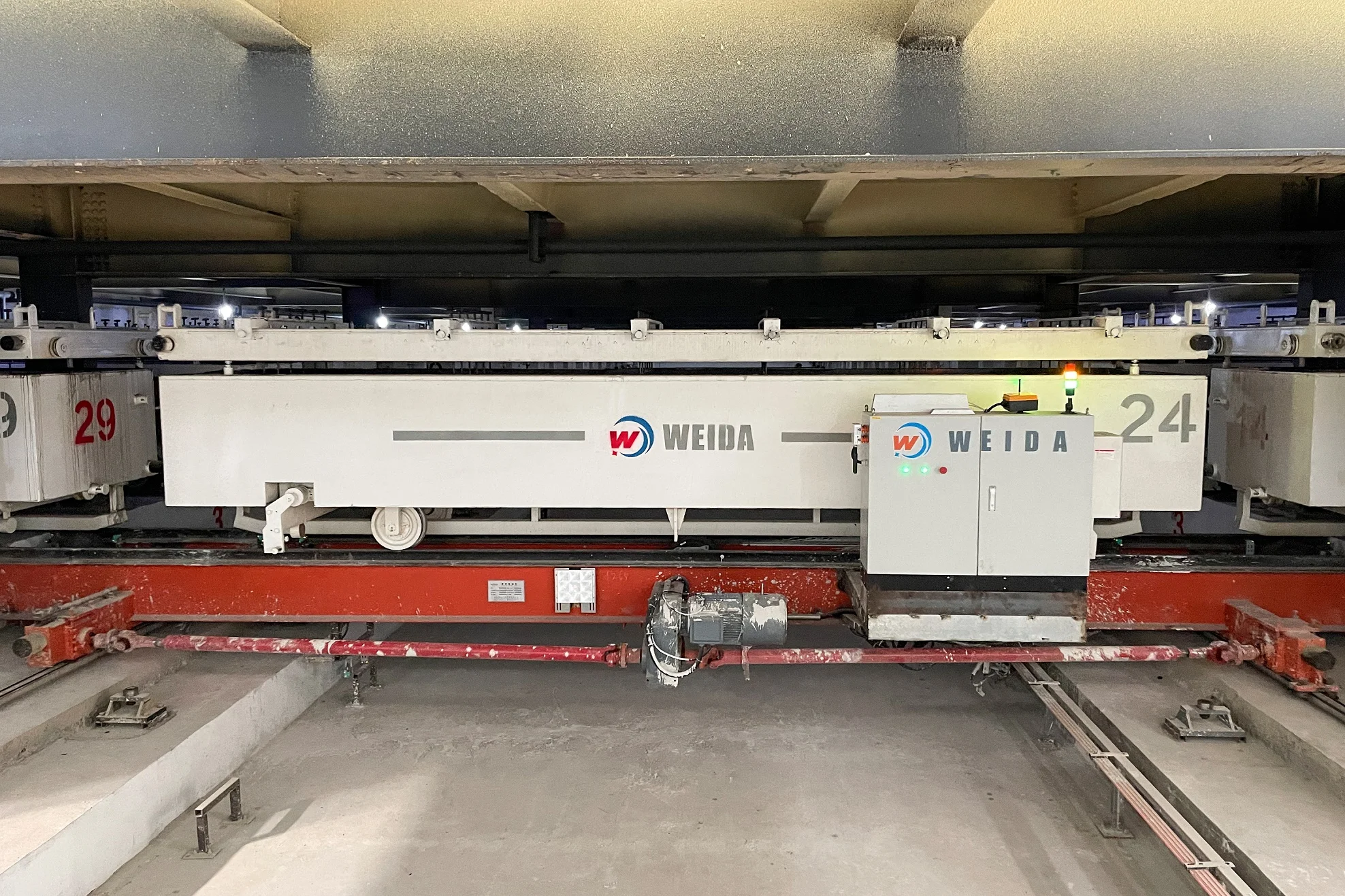
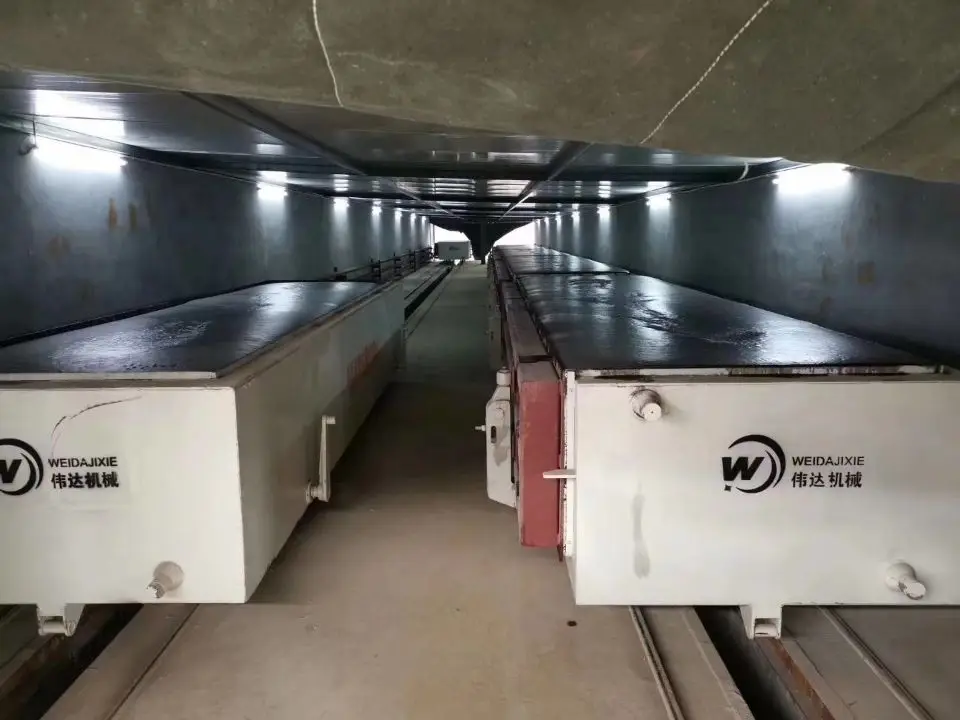
Aac Brick Manufacturing Plant Cutting process.
Using reversal crane carry the into cutting cart position for demould, after demould , The cutting cart will take the block to two sides cutting, level cutting machine, vertical cutting, , and remove the top waste and bottom waste
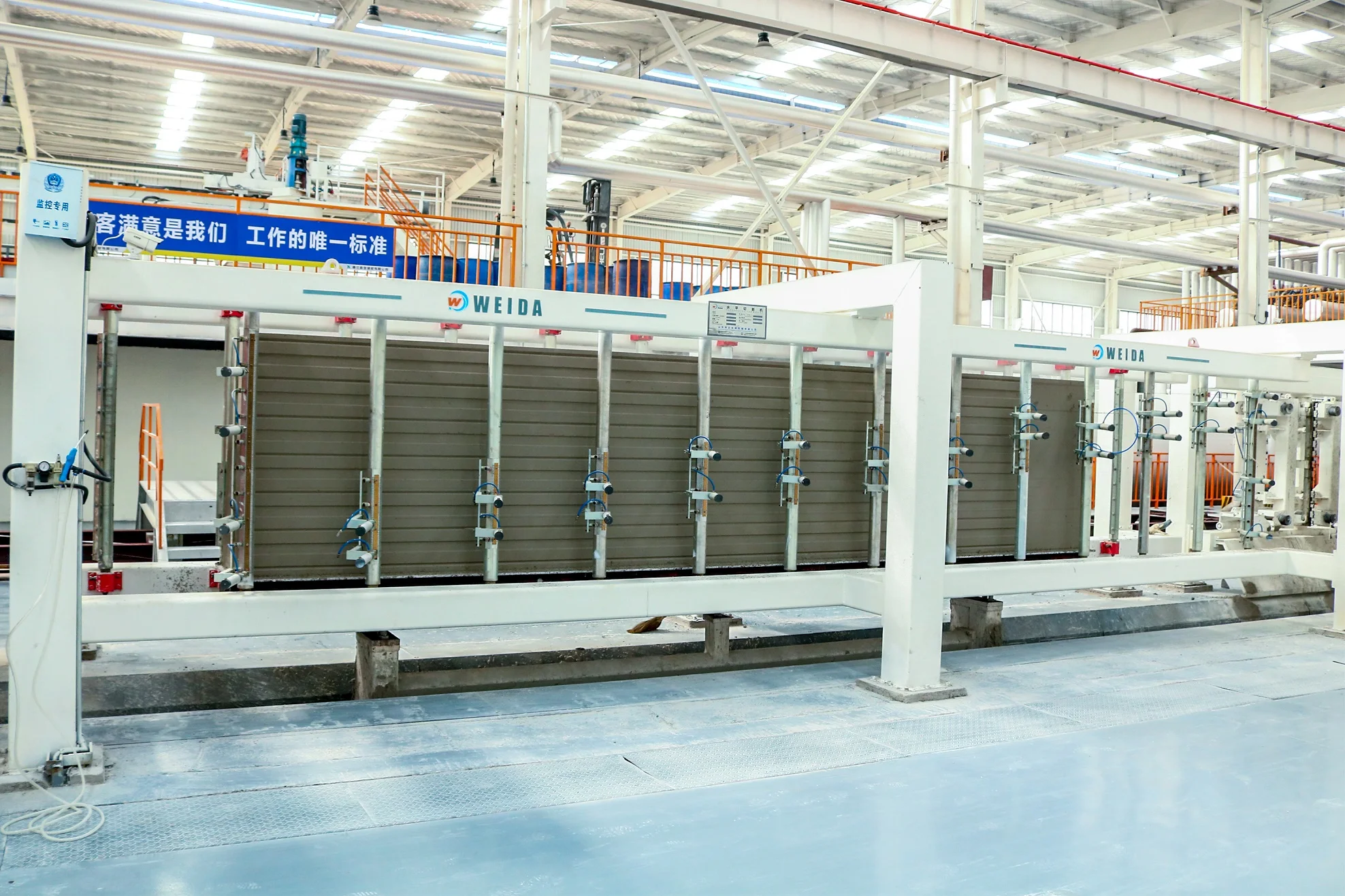
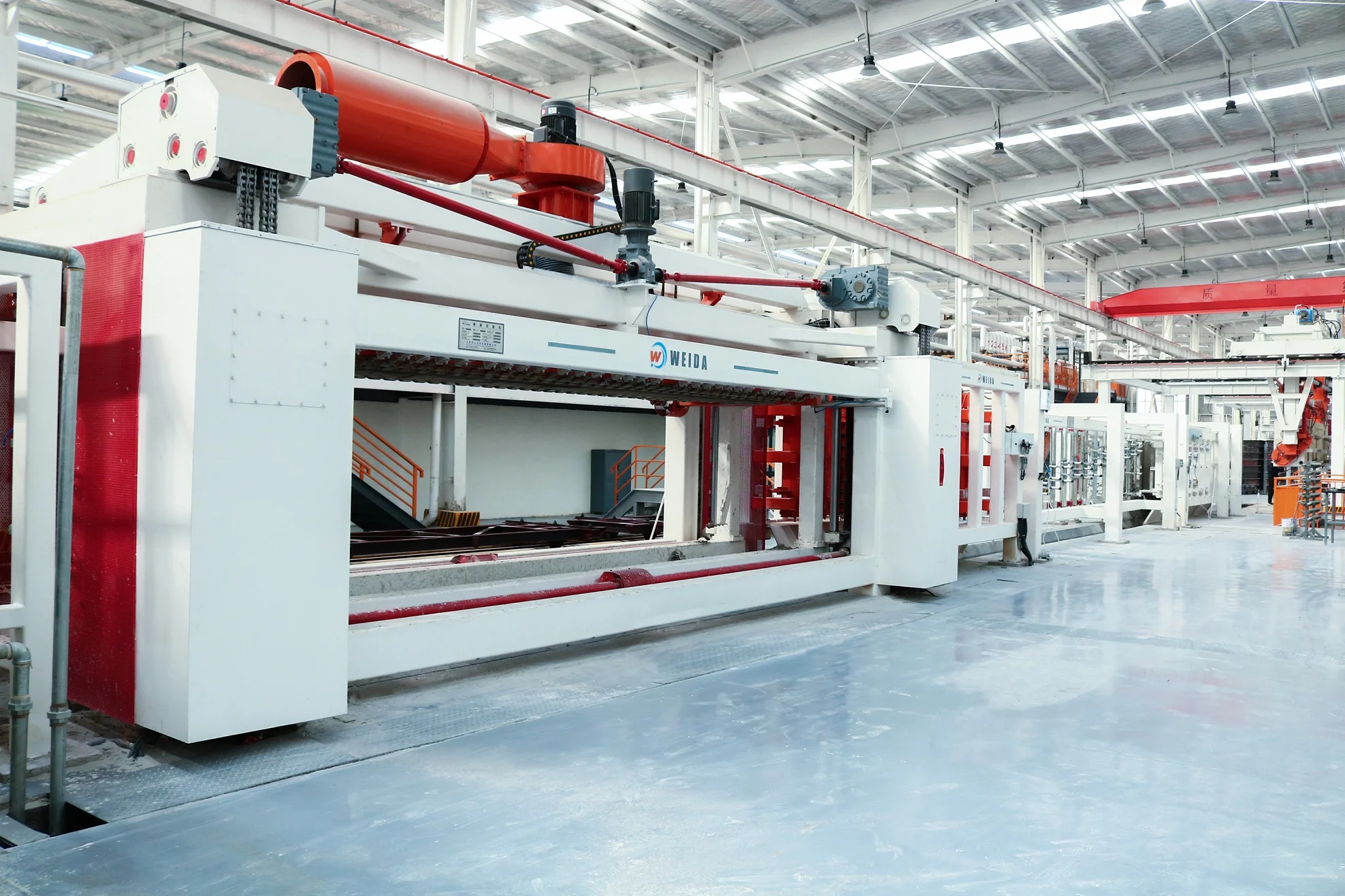
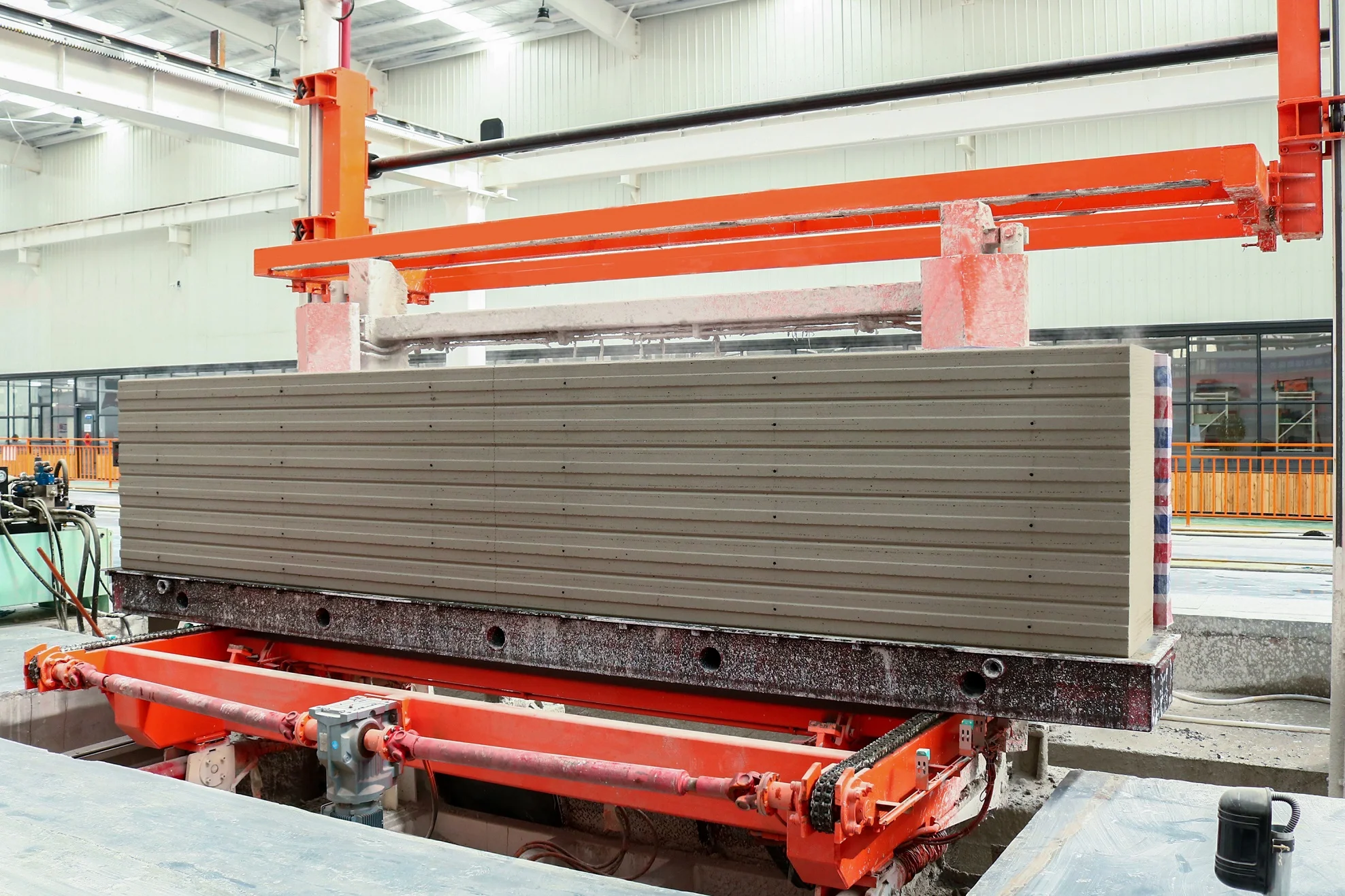
Automatic Aac Panel Production Line Autoclaved.
Finished cutting semi-product move to the front of autoclave grouped, using drag steam trolley into autoclave to steam, it need 6-11 hours , depends on the AAC block or or ALC panels
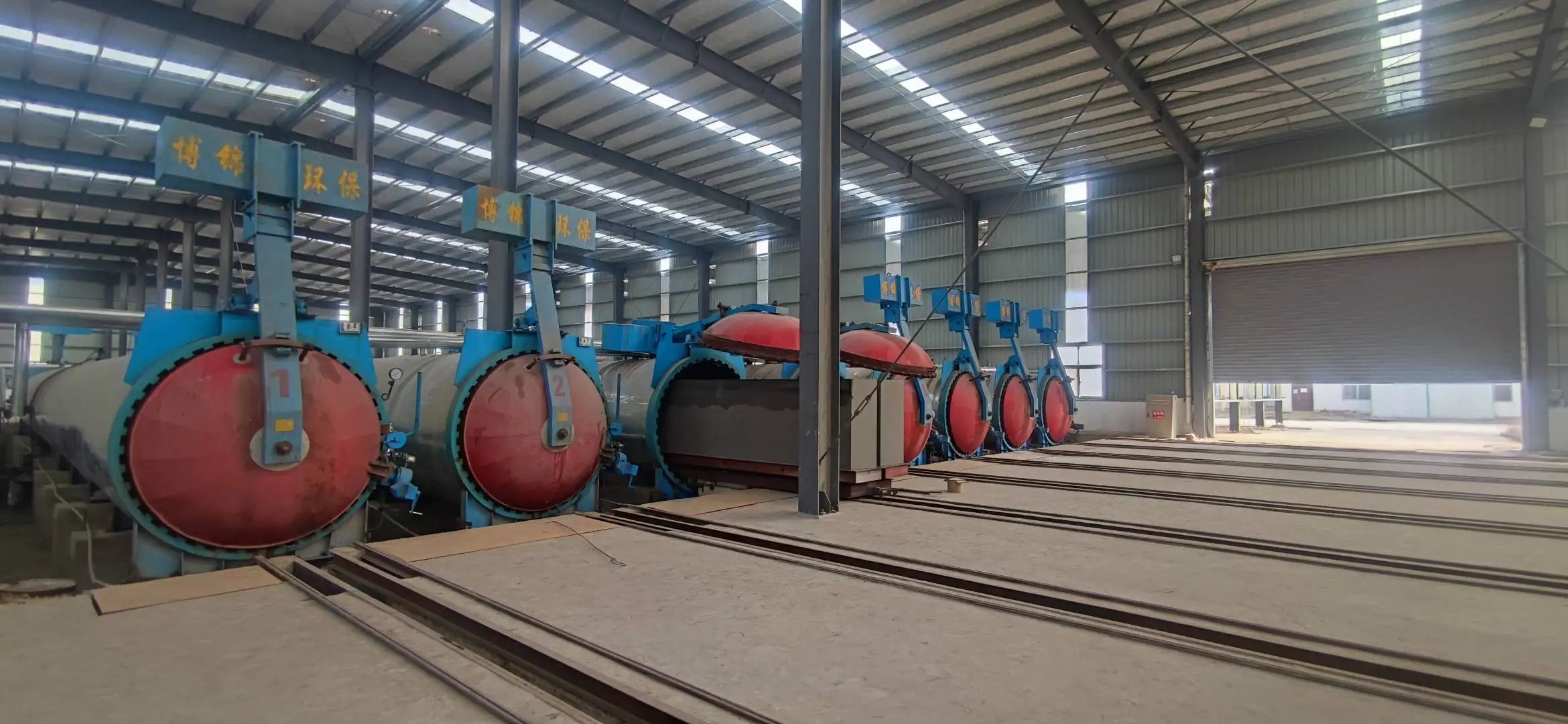
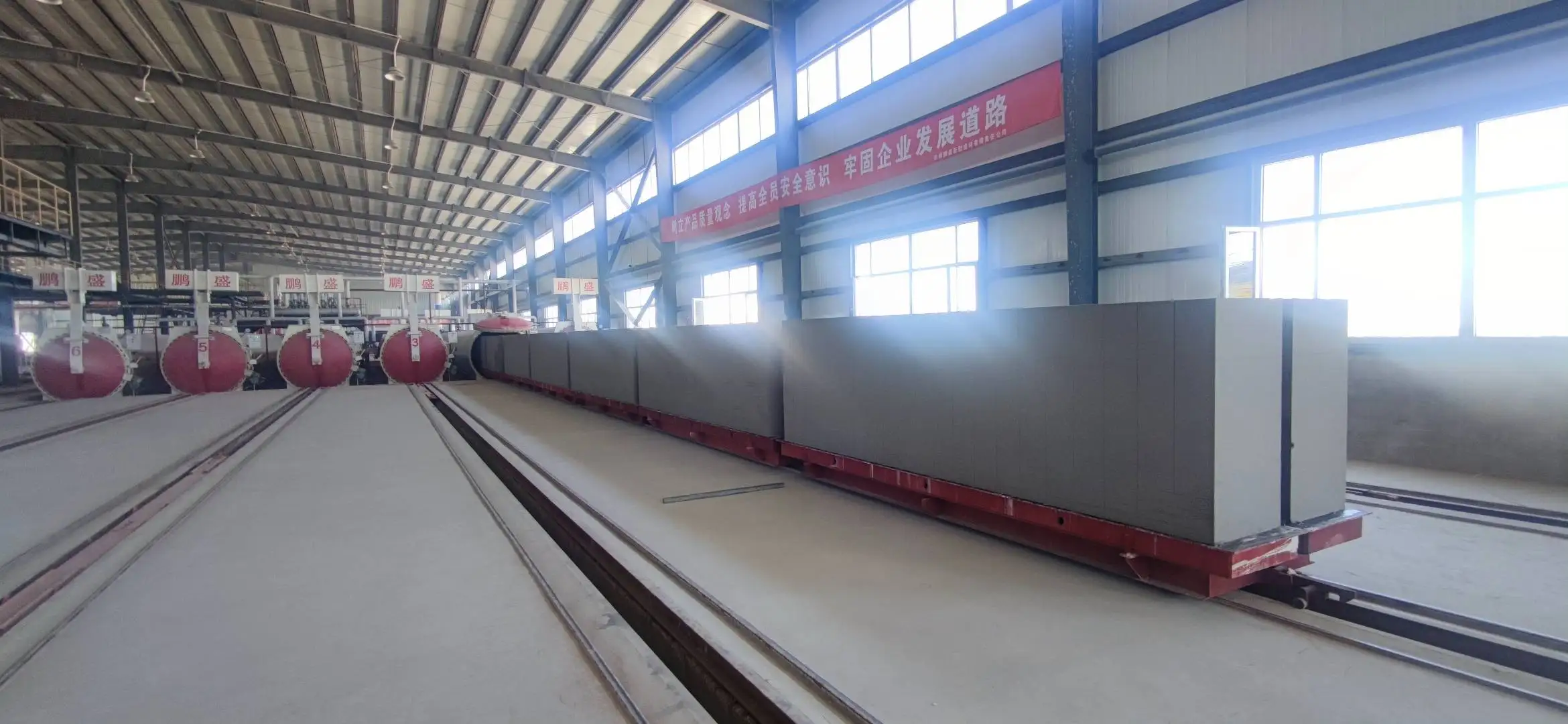
Aac Brick Manufacturing Plant Finished block dealing and package.
Finished product out of autoclave, by separating machine to separate layer by layer.
And using finished block carry clamp the finished product to package line on wooden pallets, after package, then by forklift transport the finished products to piled yard according to specifications to stack.
And using finished block carry clamp the finished product to package line on wooden pallets, after package, then by forklift transport the finished products to piled yard according to specifications to stack.
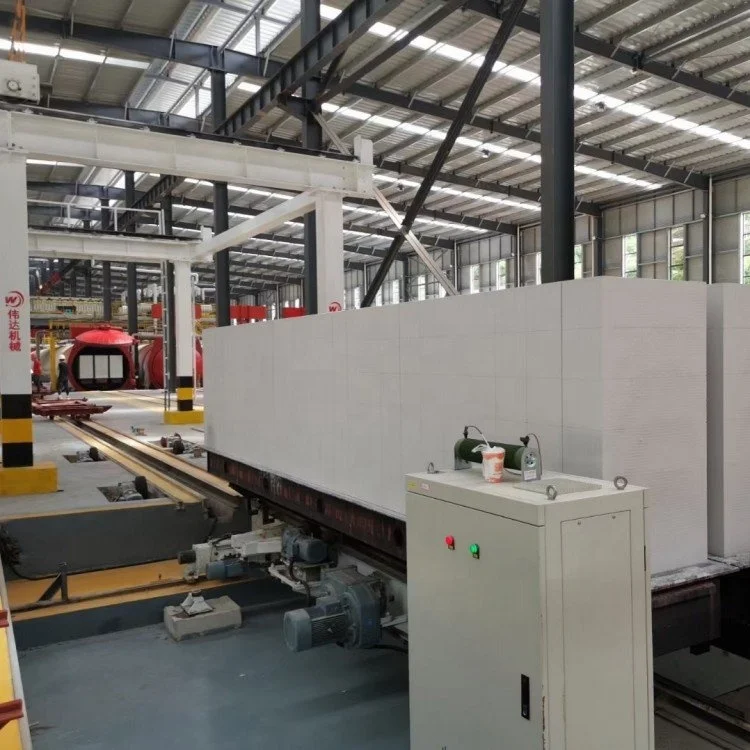
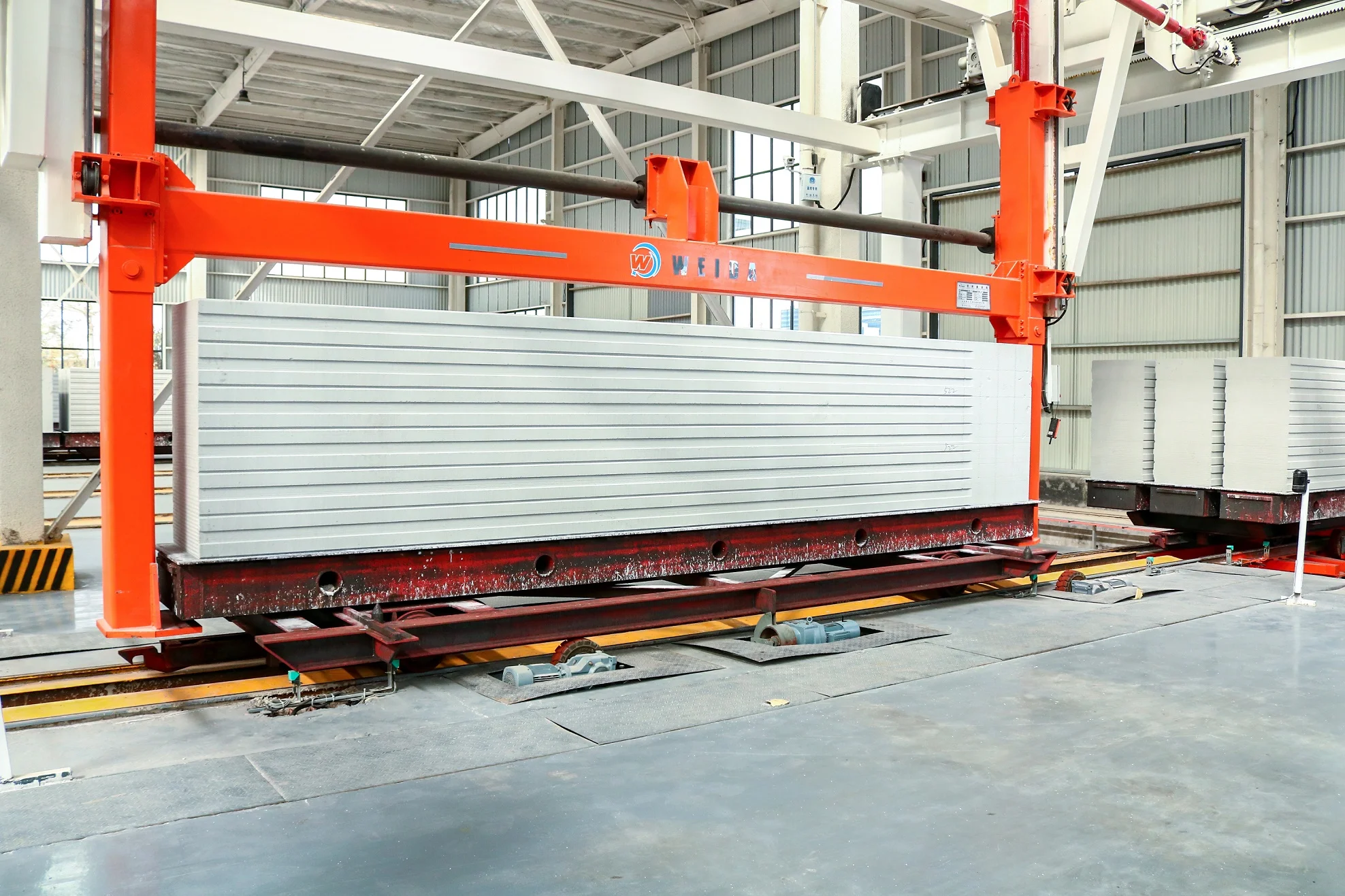
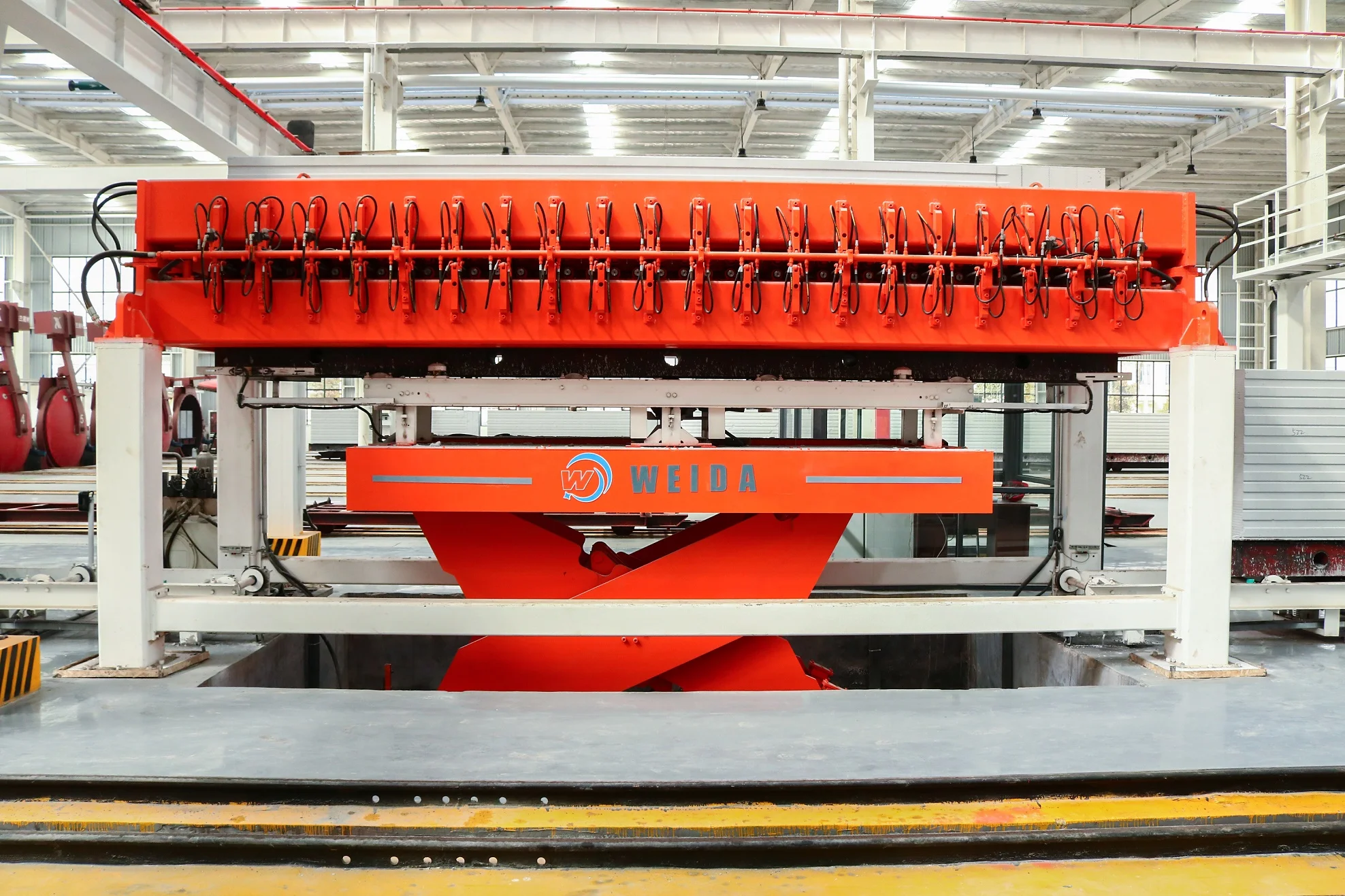
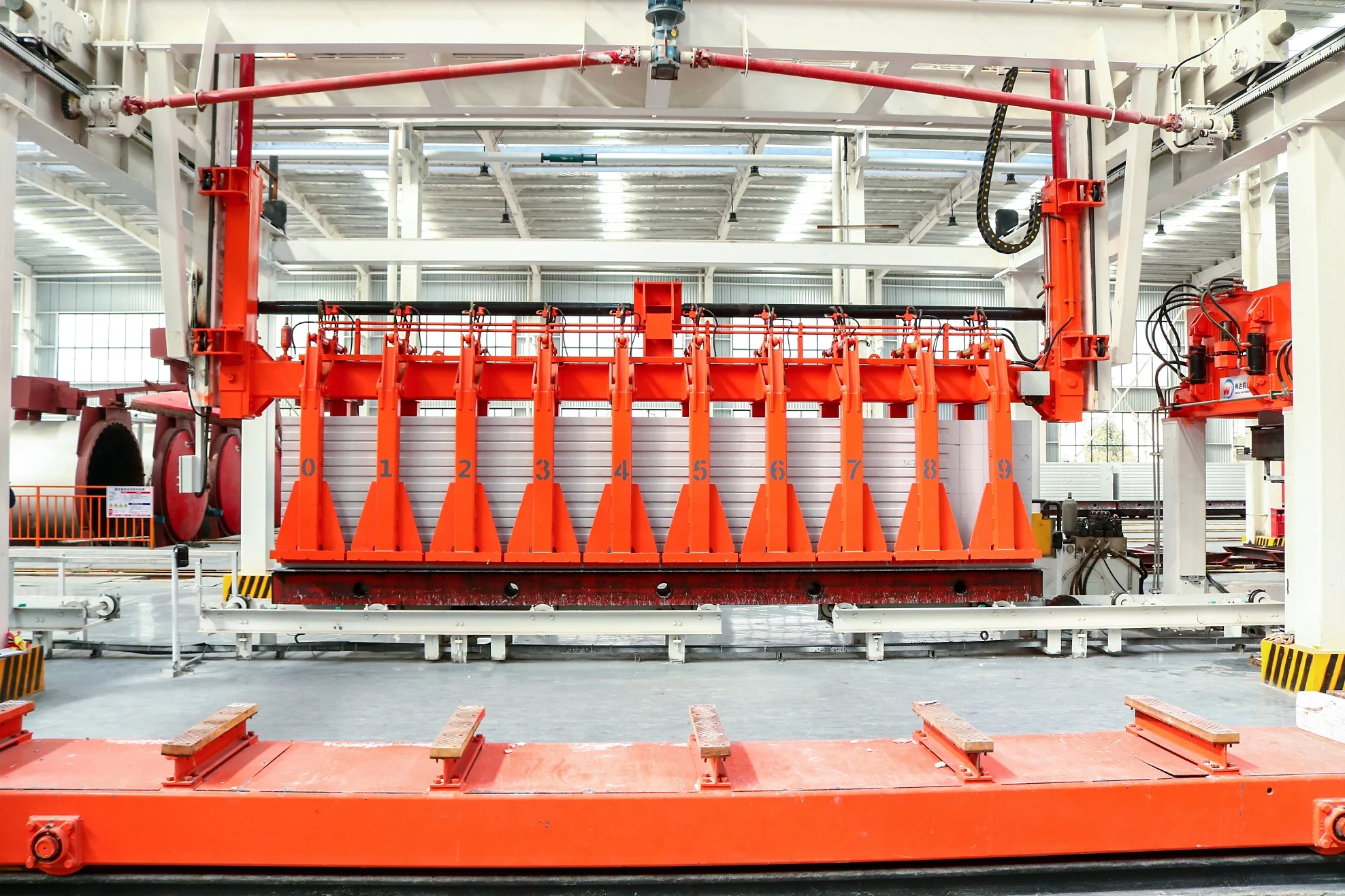
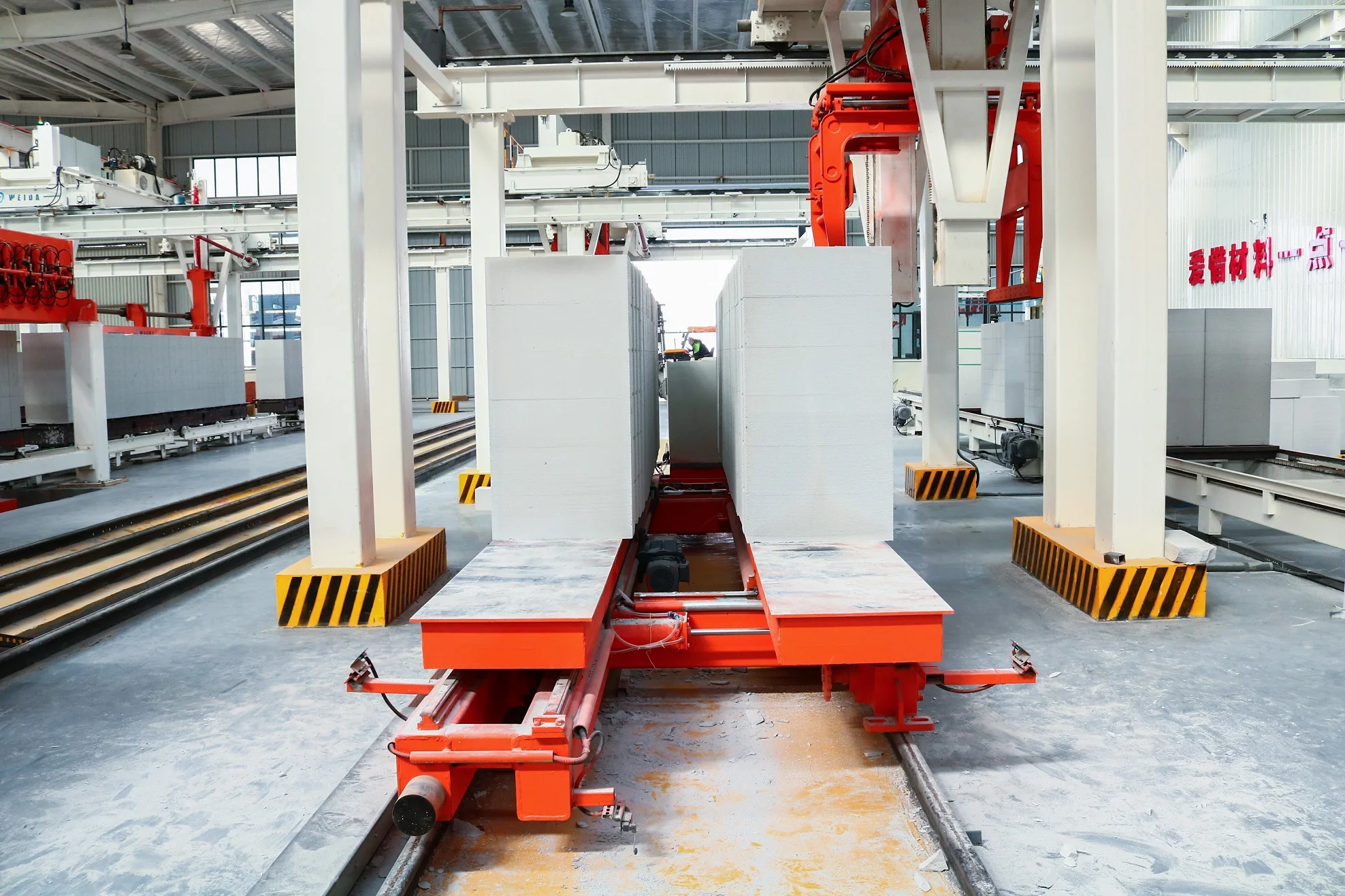
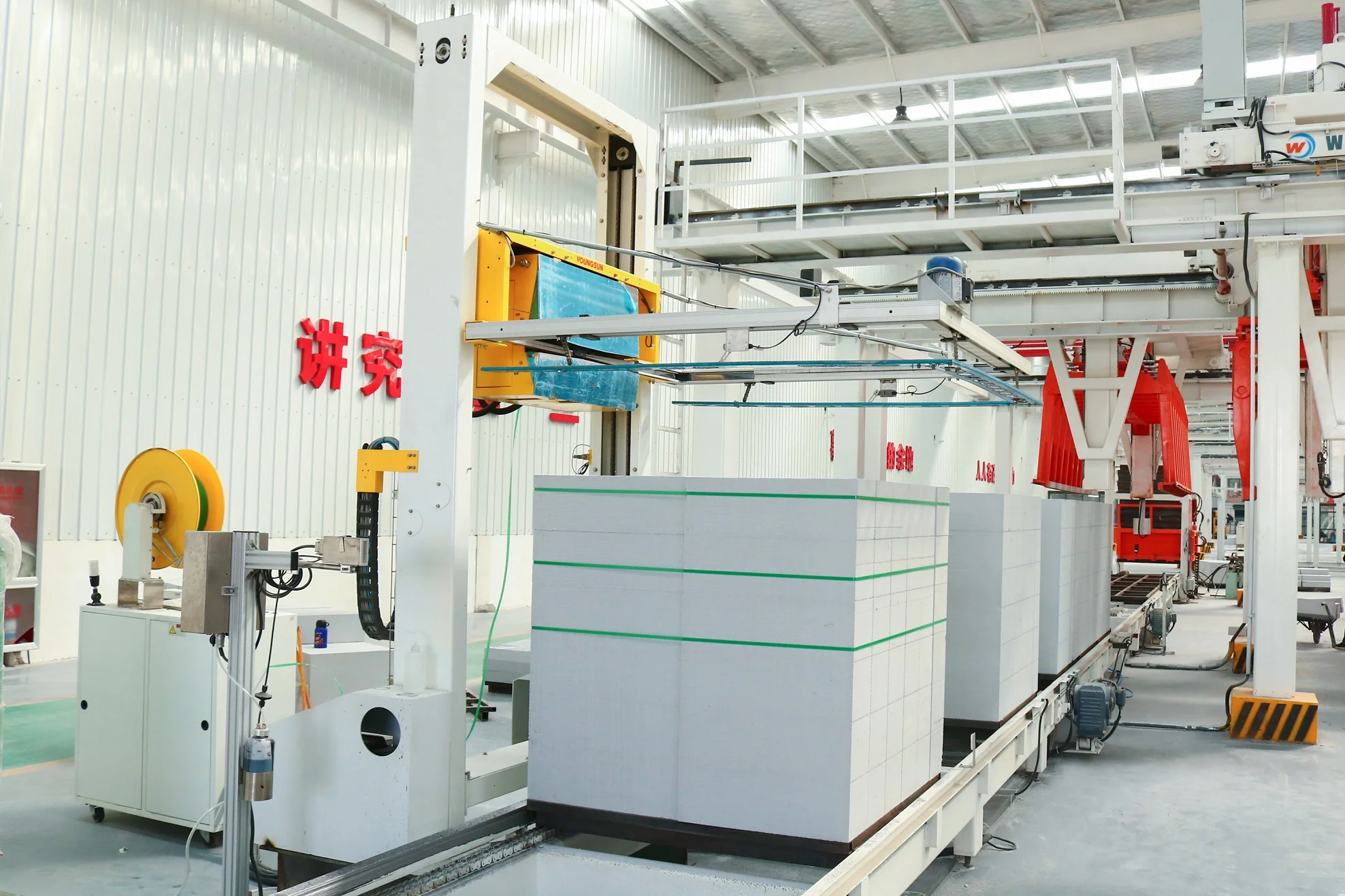
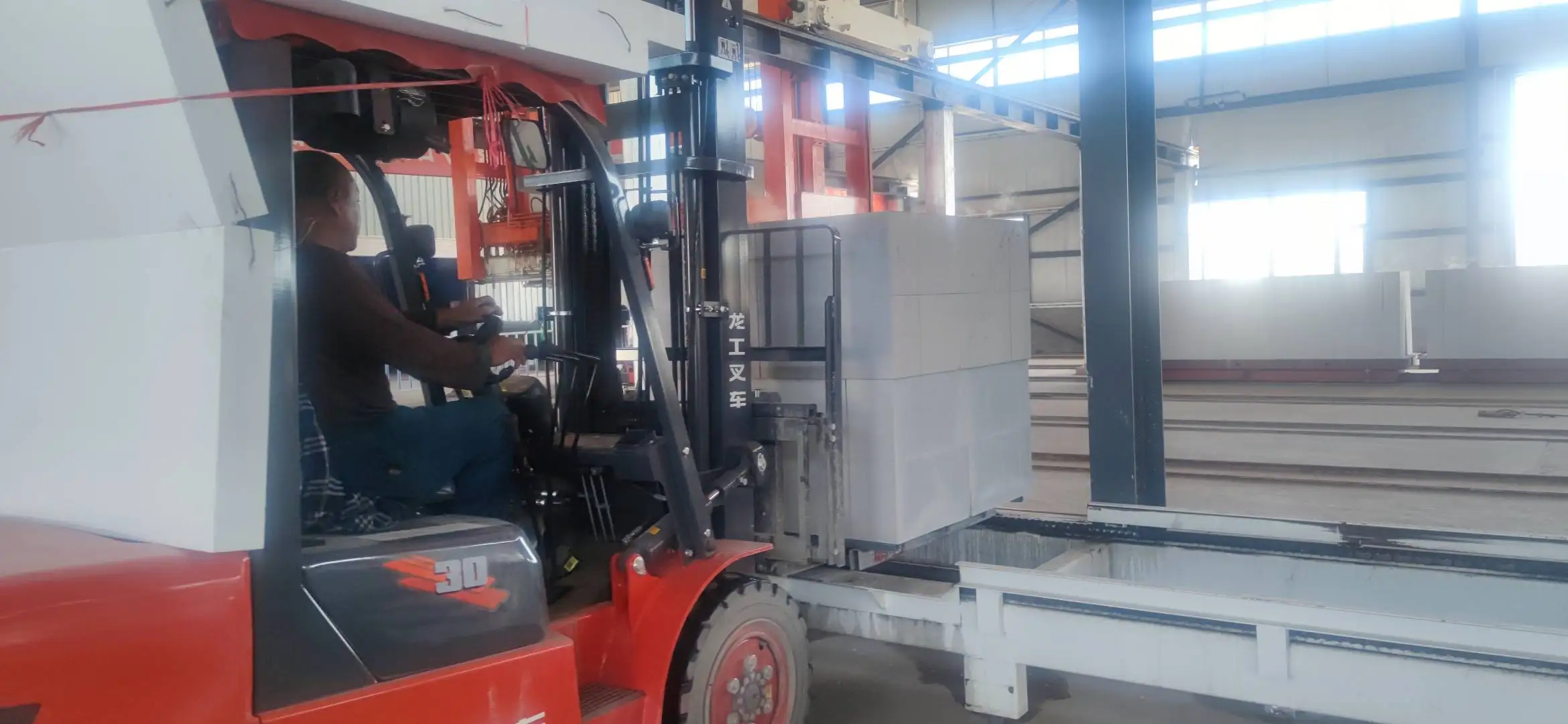
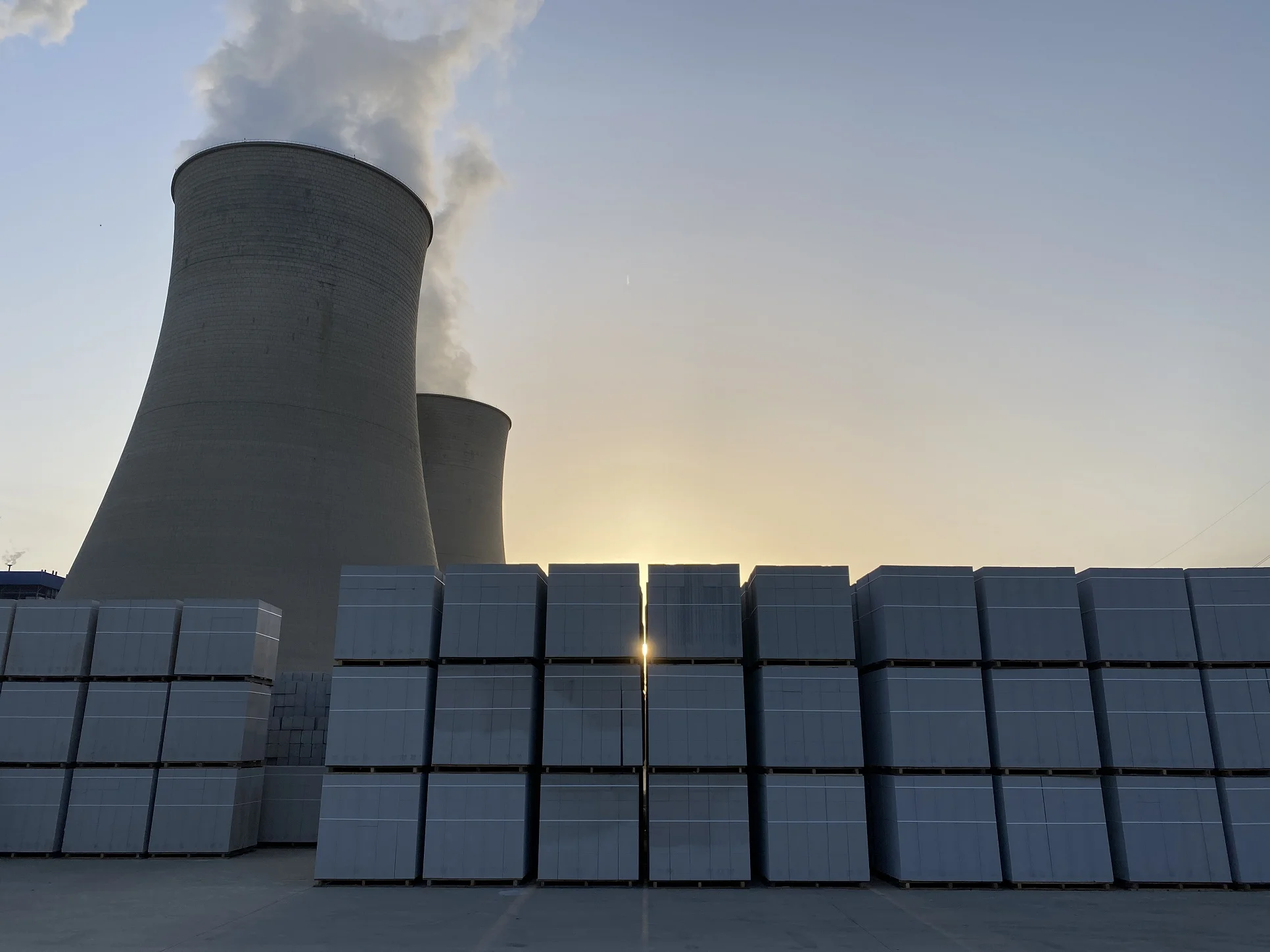
Aac Panel Production Line
AAC is a kind of light cellular silicate products.
Main material based on Silicon materials (sand, fly ash, gangue contains silicon) and Calcium (cement and lime), mix with foamingagent (Aluminium powder), after batching, mixing, pouring, pre-curing, cutting, steam (autoclaved), and other process, finally,get this light weight concrete products.
Main material based on Silicon materials (sand, fly ash, gangue contains silicon) and Calcium (cement and lime), mix with foamingagent (Aluminium powder), after batching, mixing, pouring, pre-curing, cutting, steam (autoclaved), and other process, finally,get this light weight concrete products.
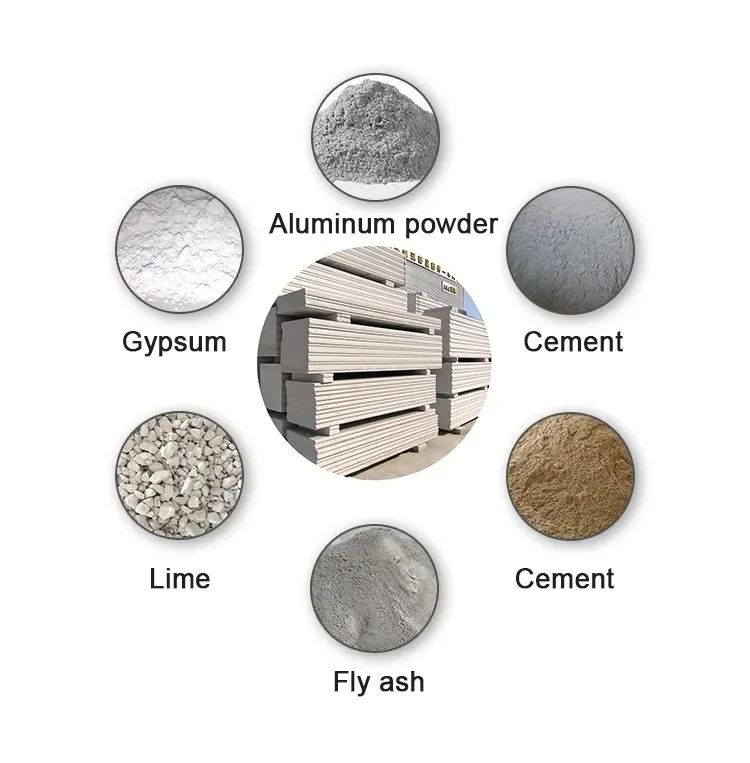
AAC blocks Advantage
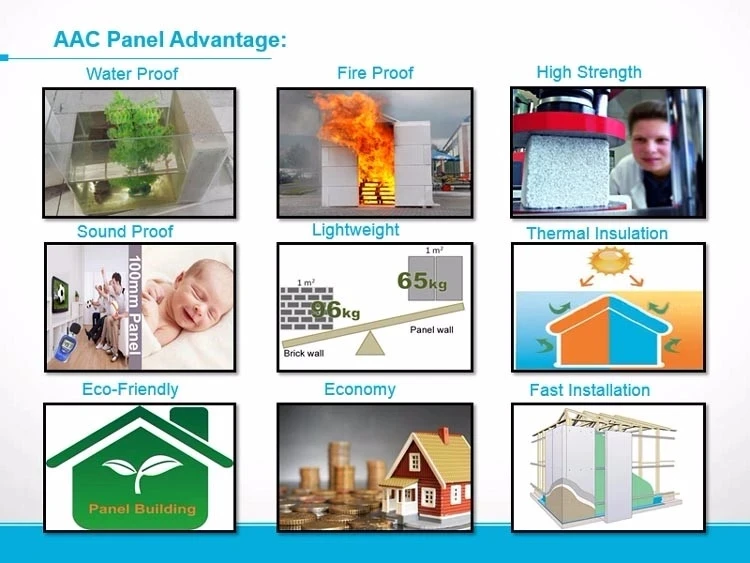
Packing & Delivery
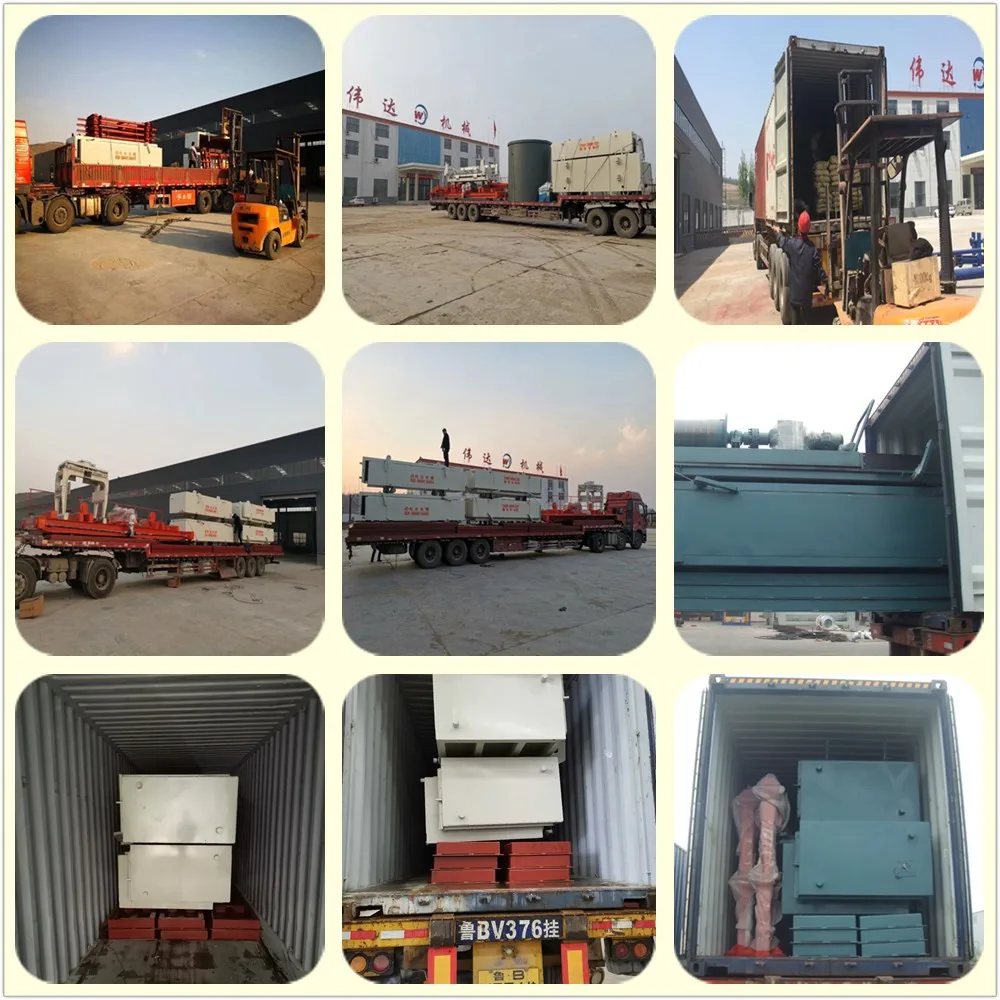
Certifications

Company Profie
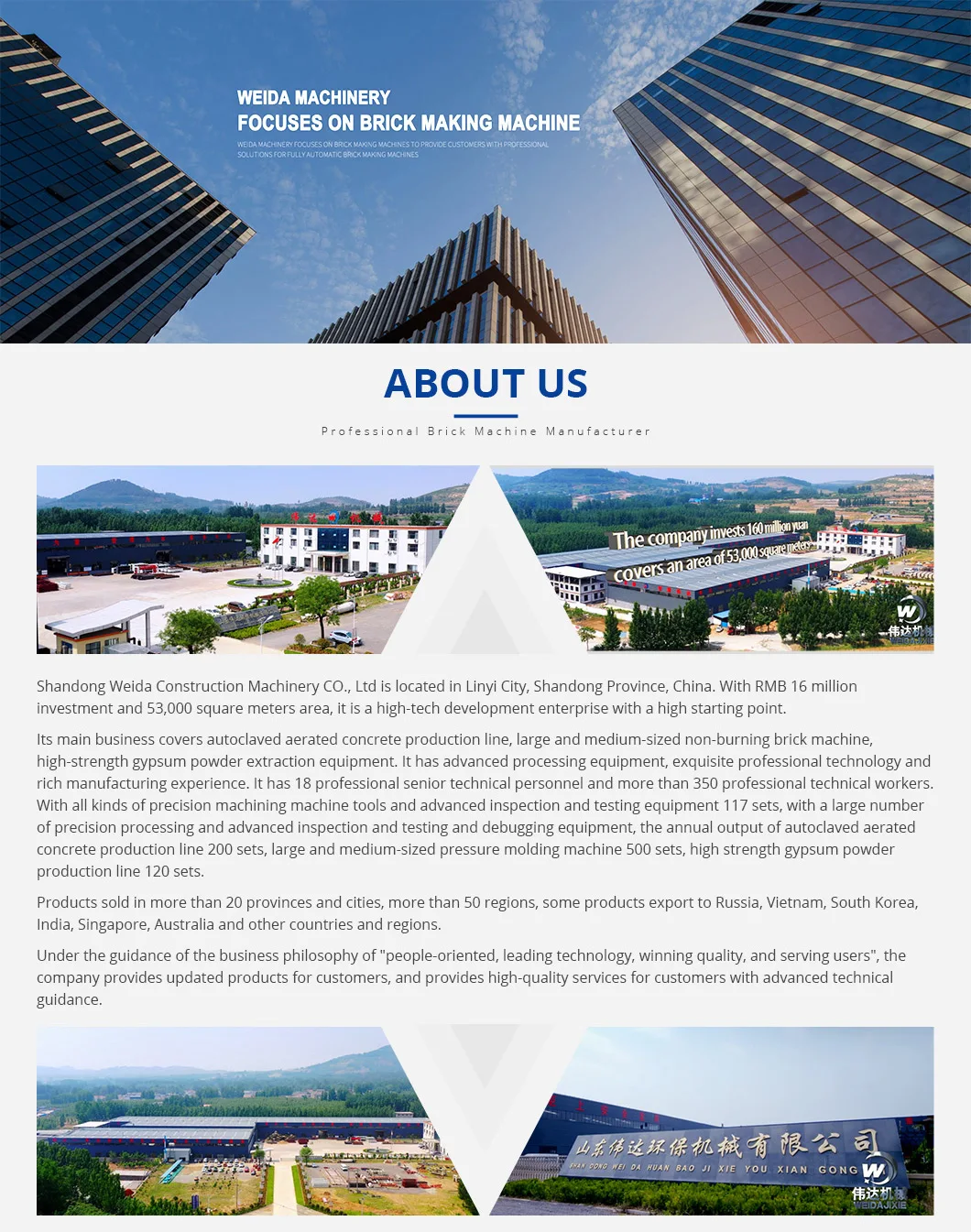
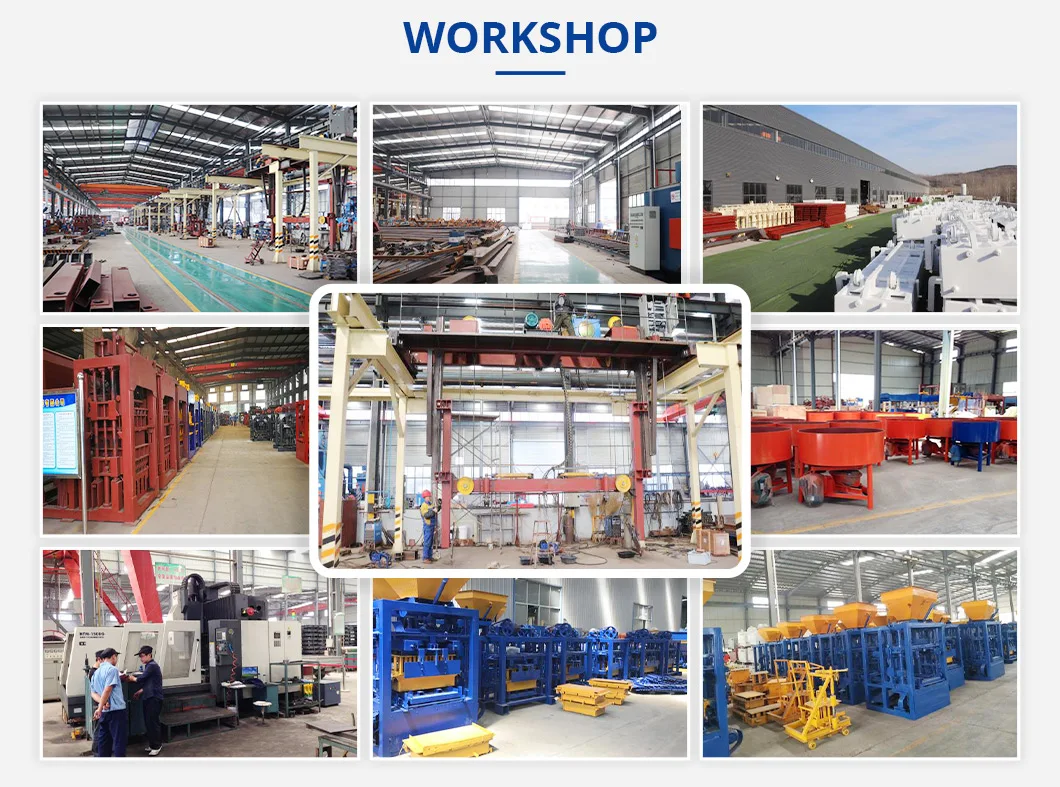
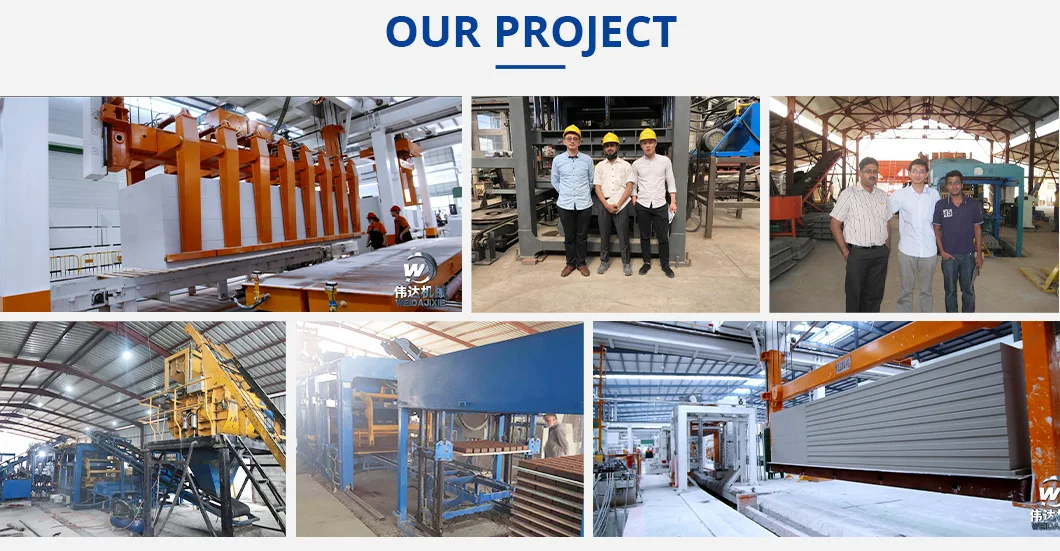
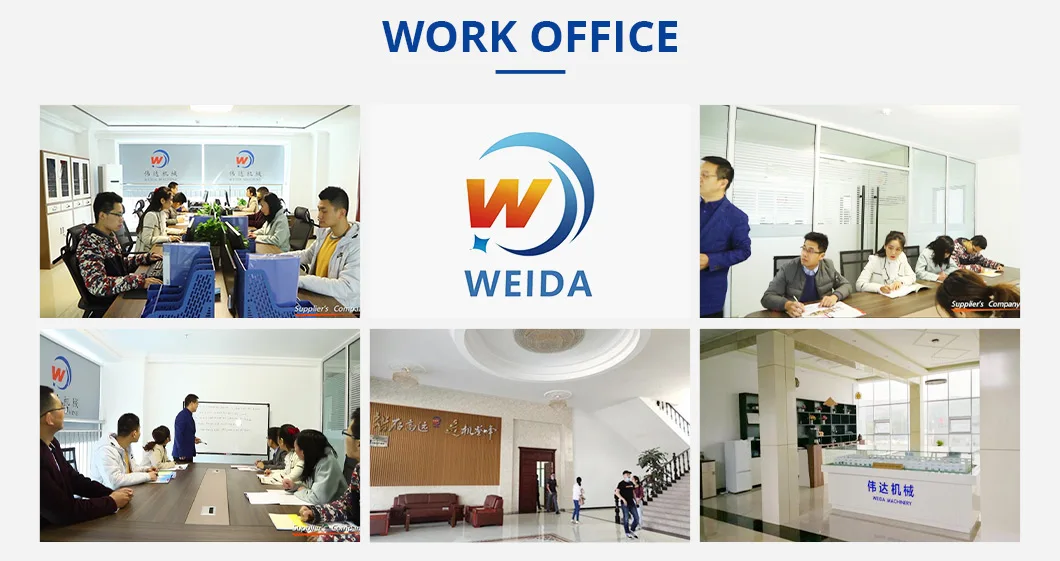
FAQ
Q1. What is the advantage about your company?
A1. Our company has professional team and professional production line.
Q2. Why should I choose your products?
A2. Our products are high quality and low price.
Q3. The logo and the color can be customized?
A3. Yes, we welcome you to sample custom
Q4. Any other good service your company can provide?
A4. Yes,we can provide good after-sale and fast delivery.