Custom Aluminum Generator diesel Stainless Steel Pressure Fuel Oil Storage tank
Other recommendations for your business
Contact us
Quik Detail
Max Working Pressure(mpa) | 1.5 MPa |
---|---|
video outgoing-inspection | Provided |
machinery test report | Provided |
core components | other |
capacity | 10-1000L |
place of origin | Guangdong, China |
brand name | OEM |
dimension(l*w*h) | Custom |
warranty | 1 Year |
key selling points | Easy to Operate |
Product Name | fuel tank |
Material | steel, stainless steel, aluminum, copper, brass, alloy etc. |
Surface treatment | power coating, plating, polishing, brushed, anodized |
Certificate | ISO9001 |
Working pressure | 0.2MPa~3.5MPa |
Processing | Laser Cutting Bending Welding |
Application | Industry |
Test pressure | YES |
Thickness | 0.80/1.00/1.20/1.8mm |
Accessories | yes |
Condition | New |
Applicable Industries | hotels, Garment Shops, Building Material Shops, Manufacturing Plant, Machinery Repair Shops, Food & Beverage Factory, Farms, Restaurant, Home Use, Retail, Food Shop, Printing Shops, Construction works , Energy & Mining, Food & Beverage Shops |
Marketing Type | New Product 2020 |
Warranty of core components | 1 Year |
Showroom Location | None |
Weight | 999 |
Product Detail

Material available | Stainless steel 201/304/316, sheet metal ( SPCC, SECC), aluminum alloy etc. | ||||||
Fabrication service | Laser Cutting ,Stamping, Punching , Bending, turning ,Welding, machining, surface treatment, and other General Fabrication Service | ||||||
Surface Treatment | Powder coating, Zinc plating, chrome plating, hot-dip, Silkscreen, polishing and so on. |
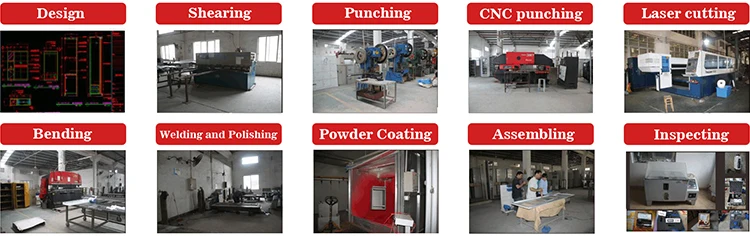
Jiangmen CNCT Co., Ltd.
founded in 2006, after 10 years of development,CNCT has become one of the most powerful large-scale sheet metal, metal products manufacturer. With over 150,000 sq. feet of manufacturing in 4 facilities. the staff more than 100 people; 10 professional engineer team, an average of more than 4 years working experience in product R&D.
ISO 9001:2008 certified CNCT utilizes ongoing employee training, automation, continuous process improvement and innovation to maximize the quality, reliability, and cost-effectiveness of your components.
Parts are carefully examined throughout the production process at multiple quality control checkpoints and all shipments are thoroughly tested and inspected before they are released to your facility. As a result, our team has been able to consistently maintain a nearly 0% external part reject rate that has enabled many of our customers to eliminate the costly and time eroding process of inbound part inspection.
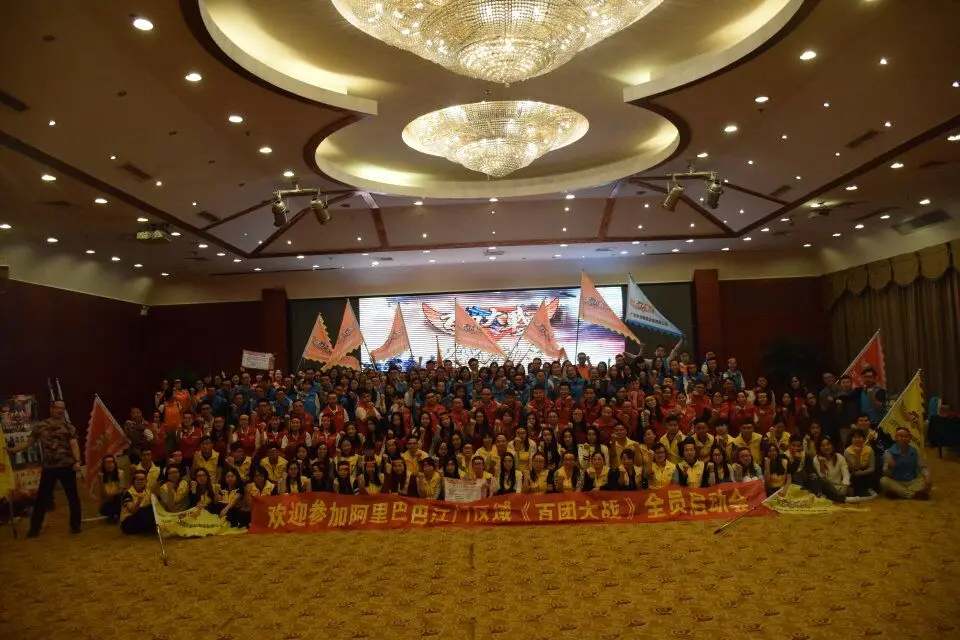
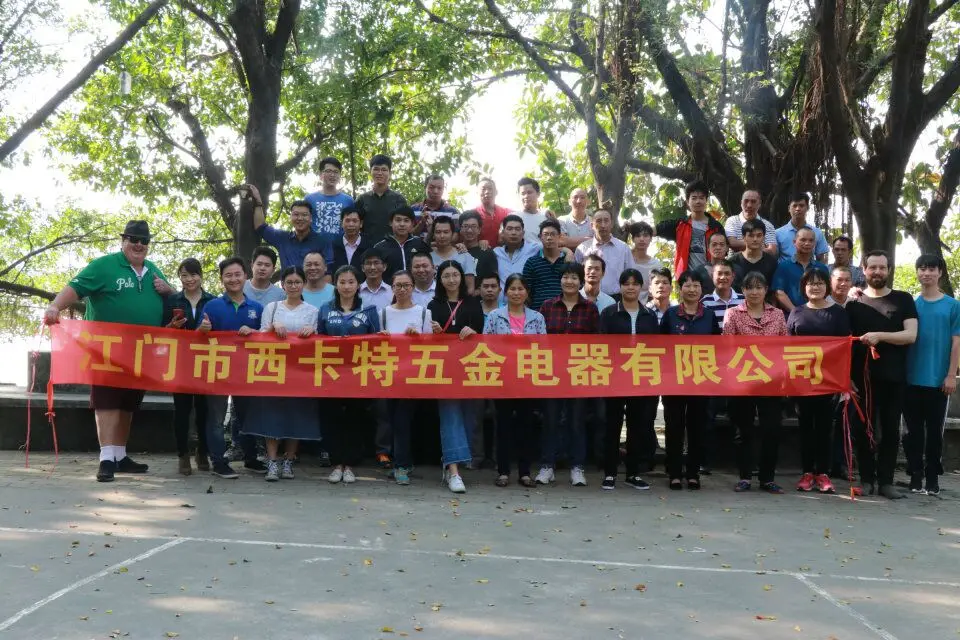
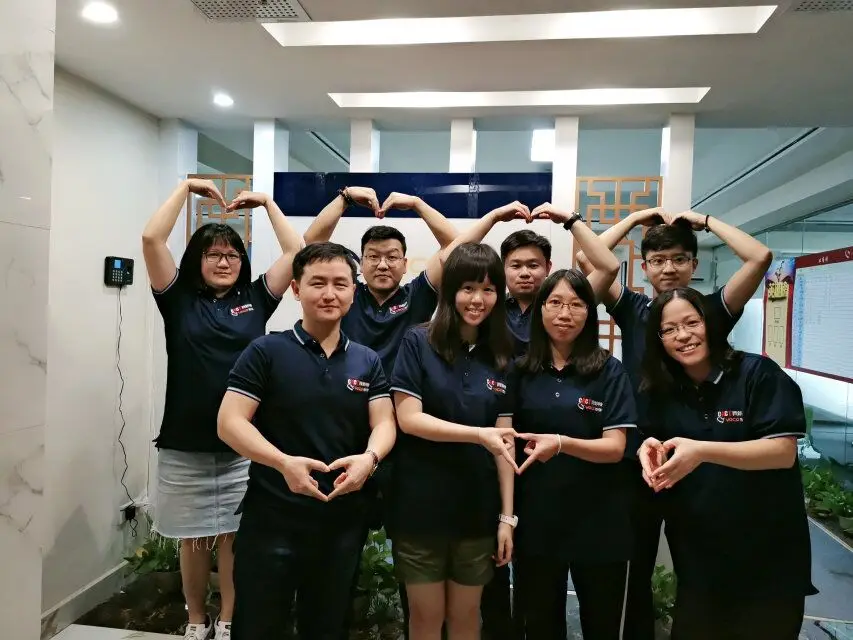
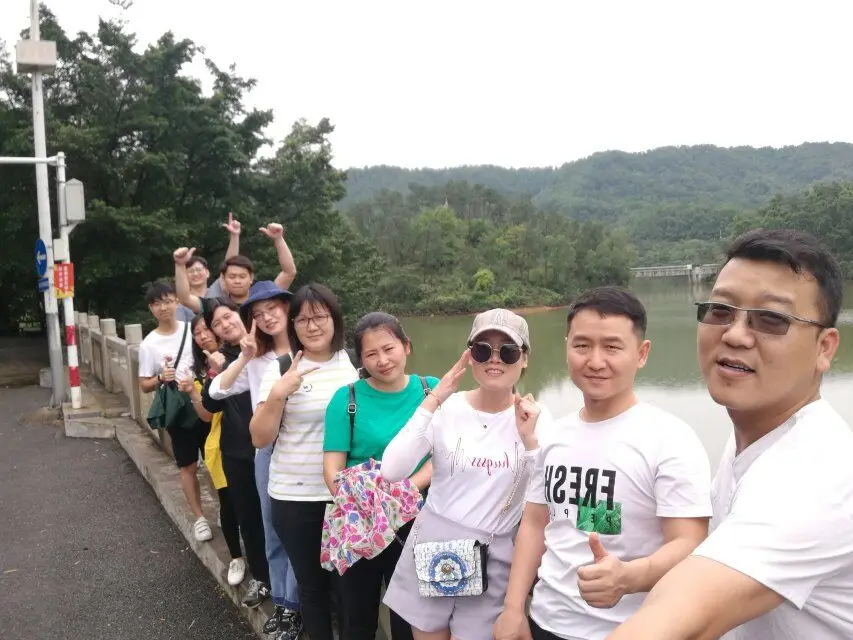
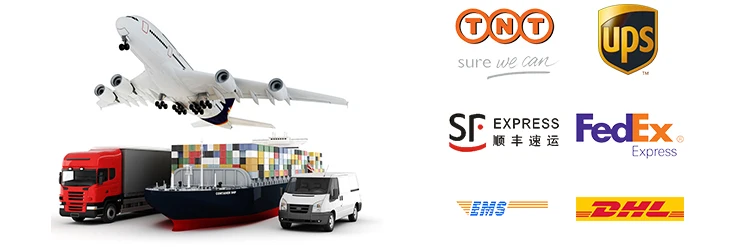

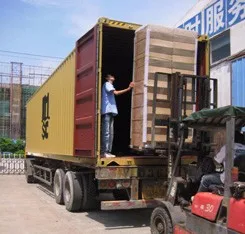
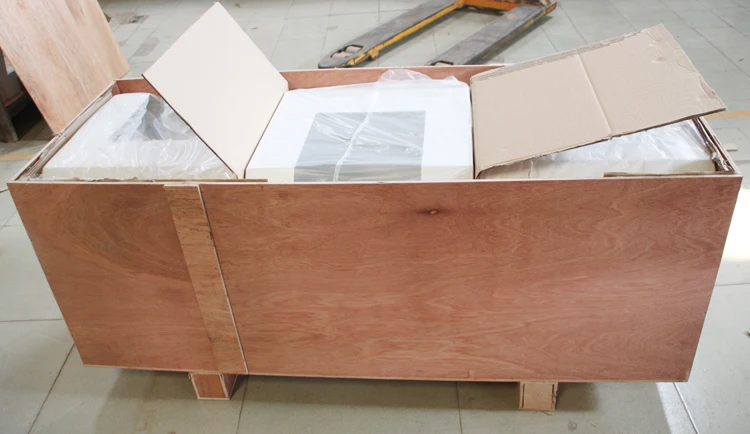
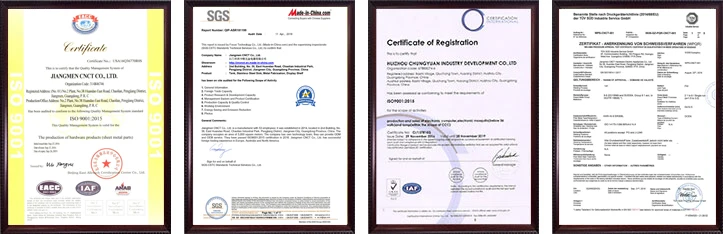
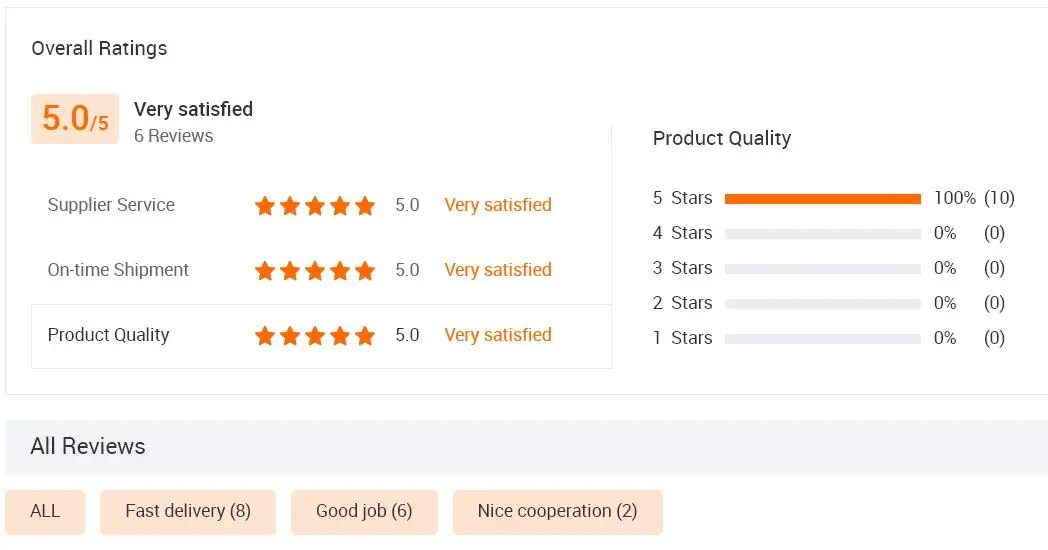

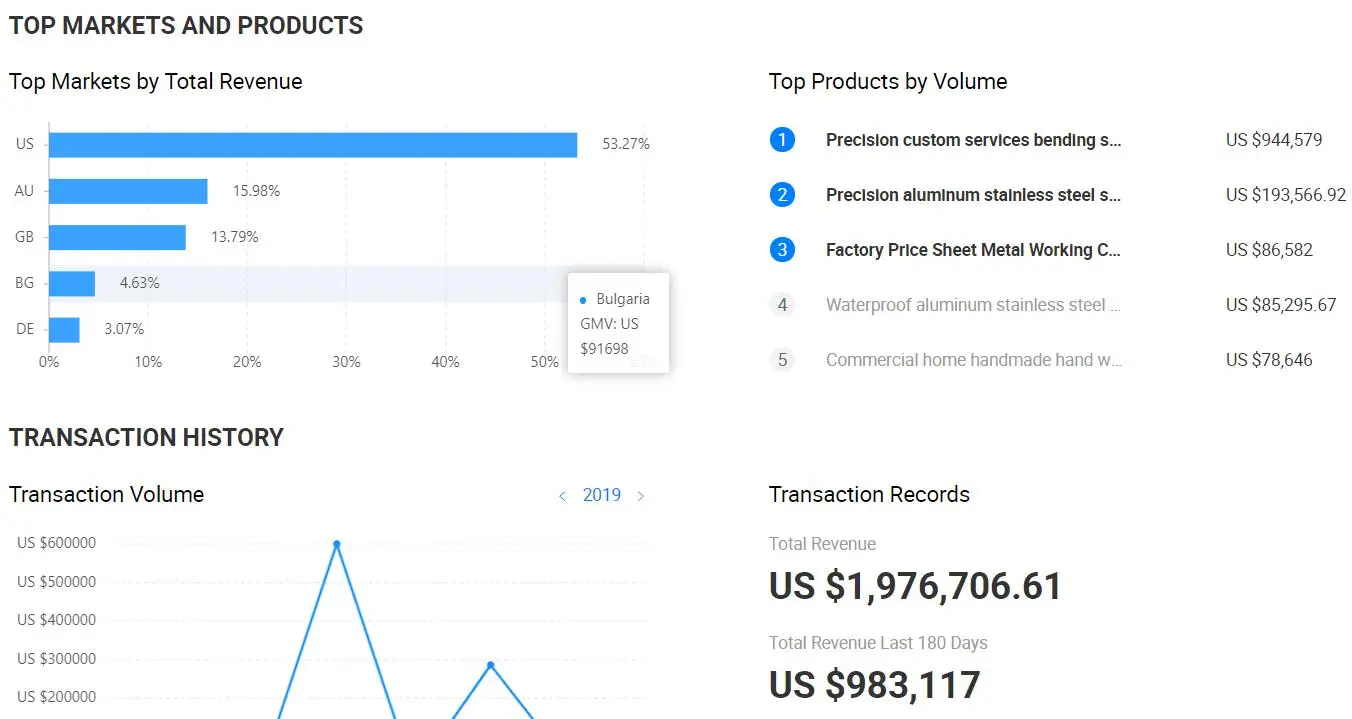