Wholesale Manufacturer Steel Degree Angle Drill Adapter For Square Drill Bits
US $6.25 / piece
10 piece(s)Minimum order
place of origin:
Taiwan, China
warranty:
Unavailable
brand name:
WEN CHIH
weight (kg):
0.032
key selling points:
Long Service Life
Material:
steel
Privacy Policy:
Samples are free within a certain price range
Other recommendations for your business
Contact us
Quik Detail
place of origin | Taiwan, China |
---|---|
warranty | Unavailable |
brand name | WEN CHIH |
weight (kg) | 0.032 |
key selling points | Long Service Life |
Material | steel |
Length | 43mm |
Inner diameter | 10mm |
Outer diameter | 16.8mm |
Thread | M8*1.25P-RH/LH |
Wrench size | 14mm |
Product Detail
Products Description
Country of origin | Taiwan, China |
Warranty period | Unavailable |
Brand | WEN CHIH |
Core selling point | Long Service Life |
Material | Steel |
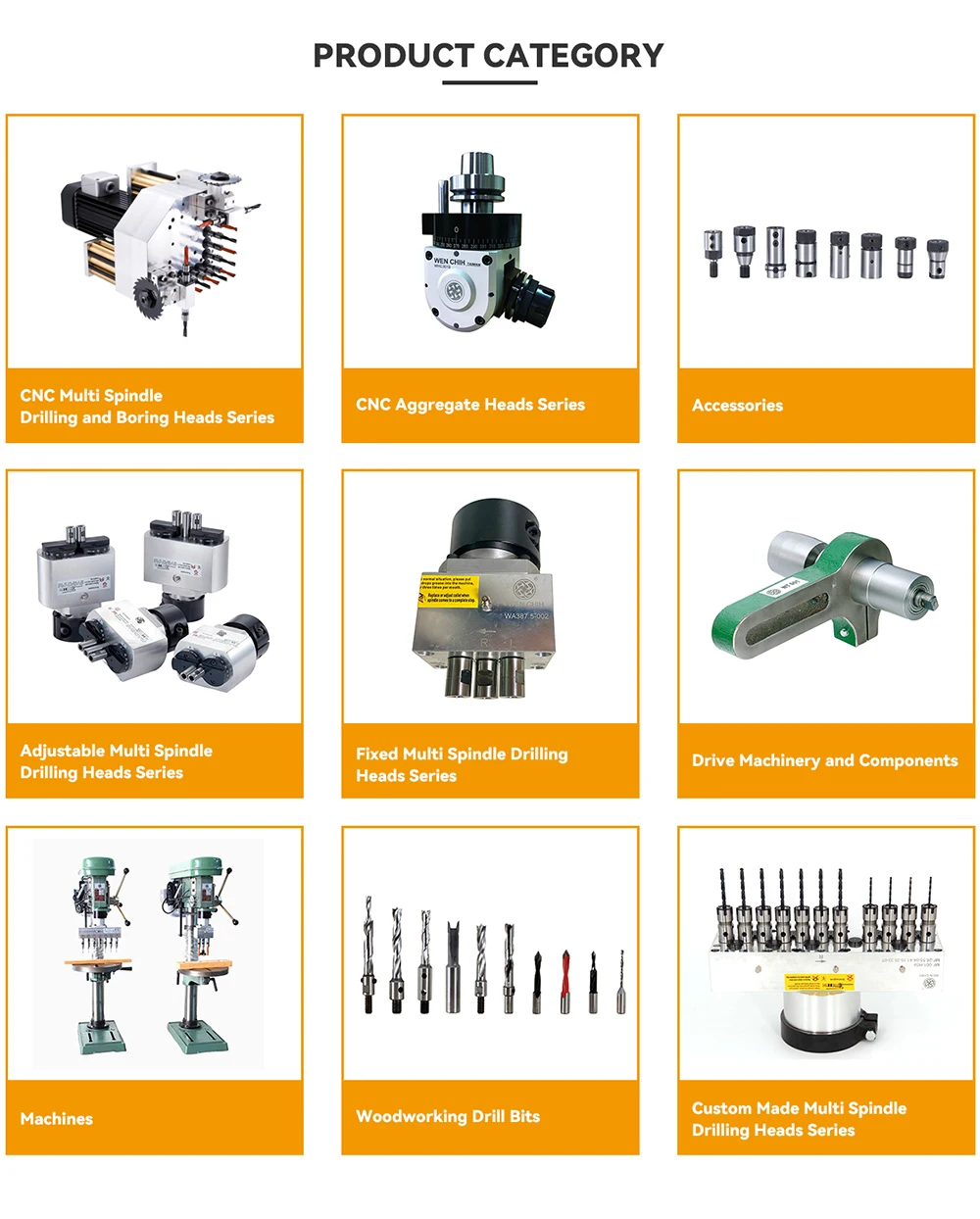
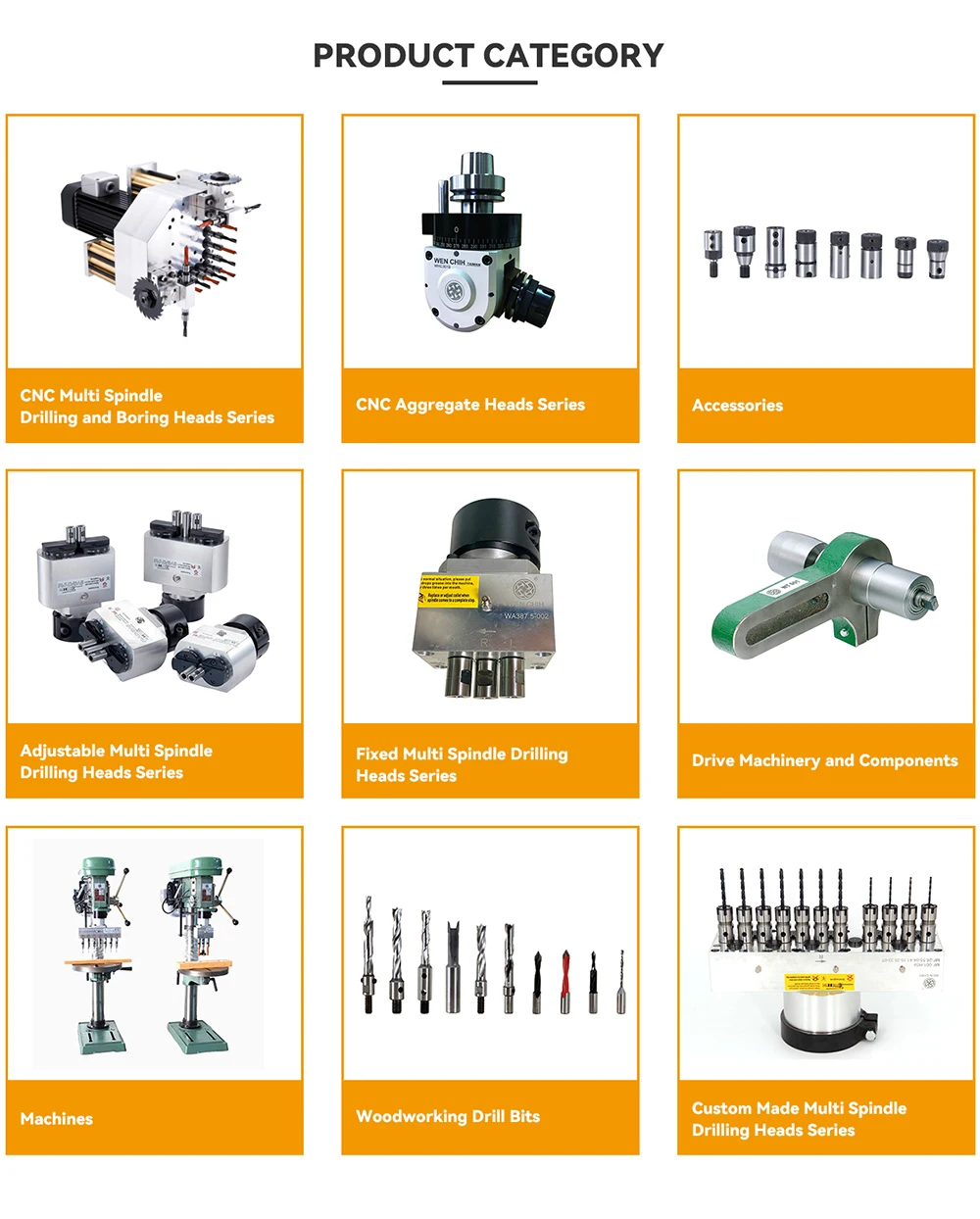
FAQ
Q1. Key Points for Using Angle Heads or Multi-Spindle Drilling Heads
Q3. Why Does the Temperature of the Angle Head or Multi-Spindle Drilling Head Rise Quickly?
When installing an angle head or multi-spindle drilling head onto a machine, ensure that all screws are securely tightened. After installation, check for any looseness or wobbling. This is crucial for both operator safety and ensuring that the machined workpiece meets dimensional accuracy.
Additionally, pay close attention to the installation position of the locating pin for the angle head. Under normal conditions,
after mounting the angle head onto the machine spindle, the locating pin should still be able to move upwards. Make sure to push it firmly into place and then check for any movement. If the head still wobbles or if it is being installed on a different machine, repeat the installation steps as needed.
A critical point to note is that if the locating pin cannot move upwards after installation, it may be too long. Although the angle head may appear stable, the tool shank and machine spindle may not be fully in contact. This improper engagement could result in abnormal operation and unwanted noise.
Q2. Why is the Spindle of the Angle Head or Multi-Spindle Drilling Head Prone to Damage?
The most common cause of spindle damage is the use of dull cutting tools or drill bits, which reduces cutting efficiency.
When the tool's cutting capability is insufficient, the spindle experiences excessive torque load, leading to potential damage.
Q3. Why Does the Temperature of the Angle Head or Multi-Spindle Drilling Head Rise Quickly?
Several factors can cause rapid temperature increases. In the case of an angle head, excessive lubricating oil buildup inside the bearings can significantly accelerate temperature rise. Over prolonged use, this can further damage the steel balls inside the bearings, leading to increased operational noise and reduced performance.
Q4. What Causes Abnormal Noise During Operation?
Abnormal noise is often related to the condition of the gears. After prolonged use, gear surfaces may wear out, causing increased clearance between them, or they may suffer from broken teeth. Checking the gears for wear and damage is recommended when abnormal noise occurs.
Q5. Why Won't the Angle Head or Multi-Spindle Drilling Head Rotate?
Q5. Why Won't the Angle Head or Multi-Spindle Drilling Head Rotate?
If the unit is unable to rotate, follow these troubleshooting steps:
Check for foreign objects – Disassemble and inspect for any debris obstructing movement.
Inspect the gears – Verify that the gears are in good condition and not jammed.
Examine the bearings – Ensure that the bearings are functioning correctly.
Assess the spindle – Check for possible spindle damage.
Check for foreign objects – Disassemble and inspect for any debris obstructing movement.
Inspect the gears – Verify that the gears are in good condition and not jammed.
Examine the bearings – Ensure that the bearings are functioning correctly.
Assess the spindle – Check for possible spindle damage.
Q6. How Often Should Lubricating Oil Be Added?
Our company’s products now use synthetic oil, which provides superior adhesion, higher temperature resistance, and longer-lasting lubrication.
✅ Lubrication for Angle Heads
Under normal operating conditions, after every 4 weeks or 160 hours of continuous use, loosen the oil filler screws on both sides and use an oil gun to inject 1–2 pumps of synthetic oil on each side to lubricate the gears. ⚠️ Do not use mineral oil to maintain optimal performance.
✅ Lubrication for Multi-Spindle Drilling Heads
Similarly, after every 4 weeks or 160 hours of continuous use, use an oil nozzle with an oil gun to inject synthetic oil.
Depending on the size of the drilling head, inject 1–3 pumps of synthetic oil. ⚠️ Do not use mineral oil to ensure stable
operation.
✅ Lubrication for Angle Heads
Under normal operating conditions, after every 4 weeks or 160 hours of continuous use, loosen the oil filler screws on both sides and use an oil gun to inject 1–2 pumps of synthetic oil on each side to lubricate the gears. ⚠️ Do not use mineral oil to maintain optimal performance.
✅ Lubrication for Multi-Spindle Drilling Heads
Similarly, after every 4 weeks or 160 hours of continuous use, use an oil nozzle with an oil gun to inject synthetic oil.
Depending on the size of the drilling head, inject 1–3 pumps of synthetic oil. ⚠️ Do not use mineral oil to ensure stable
operation.